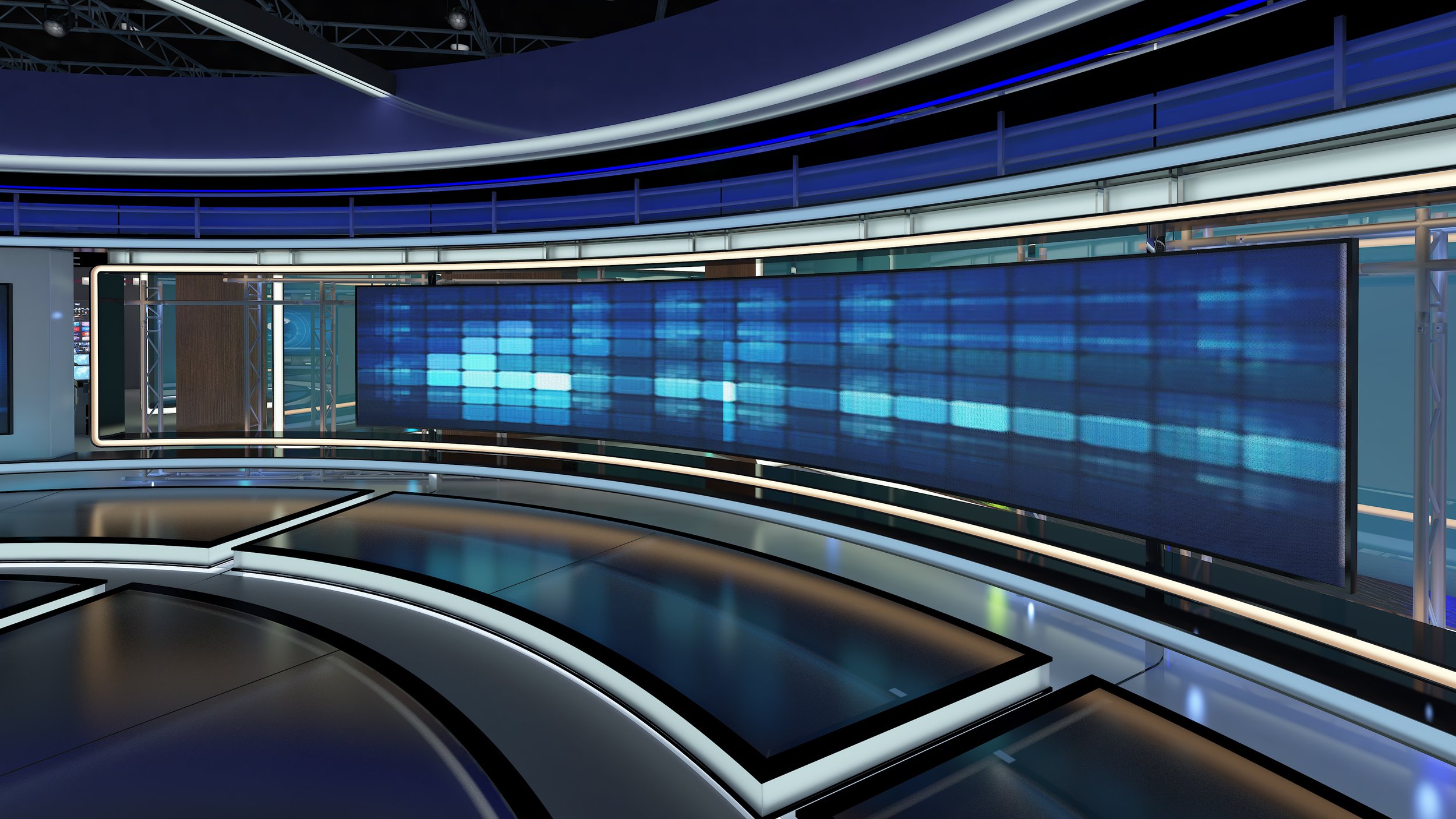
Industry News
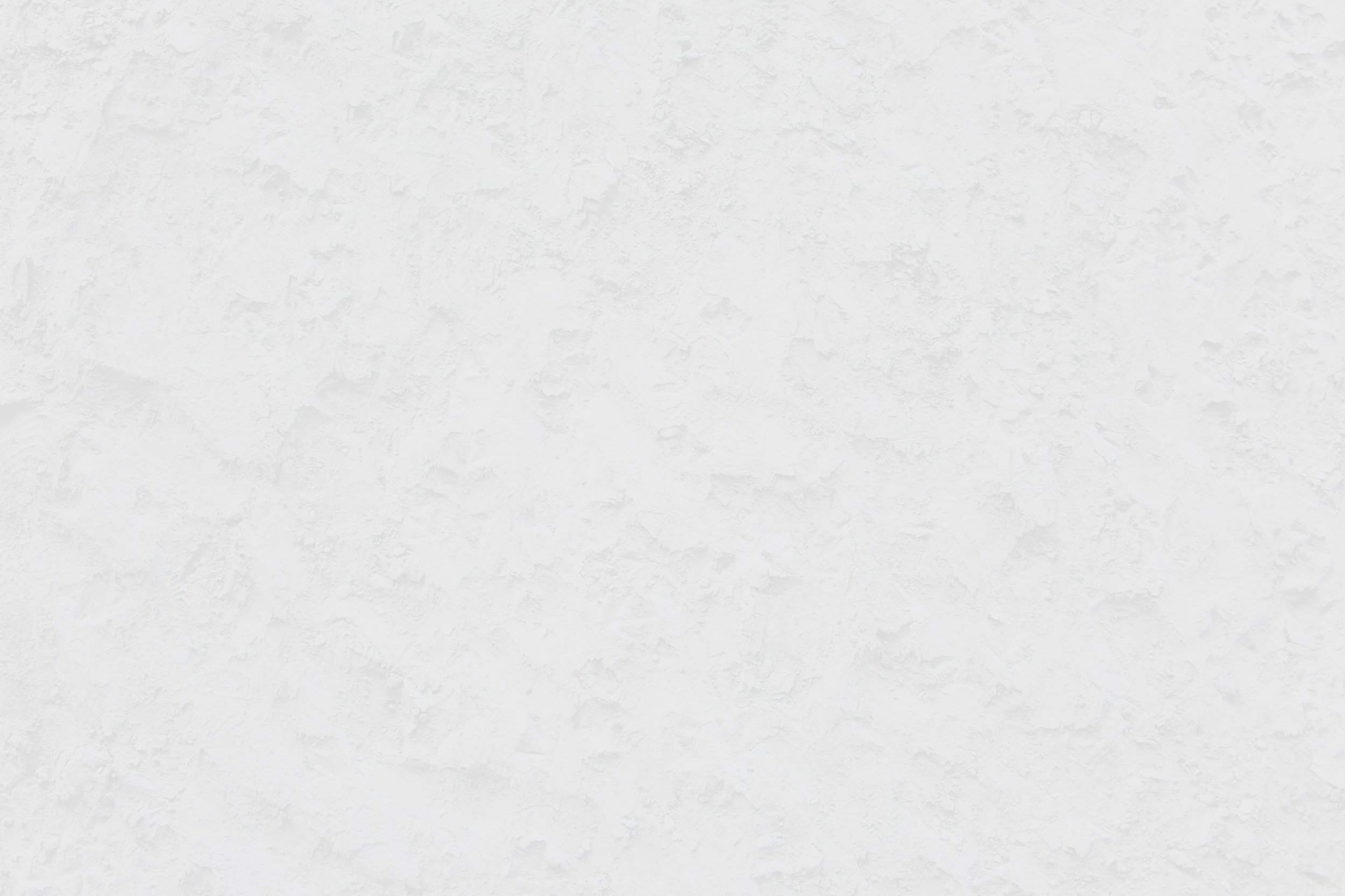
It’s OSHA 300A Time
Author, Emily Marasso, Media Communications Assistant, Rancho Mesa Insurance Services, Inc.
The holidays have come and gone and here we are at the end of another great year. Year-end means calendar updates, process changes and document reviews, as well as time to prepare for filing your OSHA 300A form.
Author, Emily Marasso, Media Communications Assistant, Rancho Mesa Insurance Services, Inc.
The holidays have come and gone and here we are at the end of another great year. Year-end means calendar updates, process changes and document reviews, as well as time to prepare for filing your OSHA 300A form.
The OSHA 300A form is a summary of injuries and illnesses which occurred on the job during the calendar year. The form must be filed electronically on the Injury Track Application (ITA) starting January 2, 2020. Deadline for 2019 data submissions is March 2, 2020. It must be displayed from February 1, 2020 to April 30, 2020.
Don’t forget, if you are a Rancho Mesa client and utilize the Risk Management Center Incident Track feature, you have access to generate the Cal/OSHA 300A form and export it to a CSV file. From there you can upload it to the OSHA website.
Rancho Mesa has put together a 5-minute tutorial video on how to generate the electronic 300A form data file from the Risk Management Center, that can be uploaded to the Injury Tracking Application website for reporting the data.
For questions about how to track the injury and illness data in the Risk Management Center, contact Alyssa Burley at (619) 438-6869.
OSHA Offers Grant Programs to Nonprofits
Author, Sam Brown, Vice President, Human Services Group, Rancho Mesa Insurance Services, Inc.
Nonprofit leaders who want to make workplace safety training more accessible may be surprised to learn about a unique grant program through the Occupational Safety and Health Administration (OSHA). Since 1978, OSHA has offered grants to nonprofit organizations for safety training. Specifically, grants are awarded on a competitive basis to provide employees with training on the recognition and prevention of safety/health hazards in the workplace. The intent of the program is to reach audiences who might not otherwise receive safety training.
Author, Sam Brown, Vice President, Human Services Group, Rancho Mesa Insurance Services, Inc.
Nonprofit leaders who want to make workplace safety training more accessible may be surprised to learn about a unique grant program through the Occupational Safety and Health Administration (OSHA).
Since 1978, OSHA has offered grants to nonprofit organizations for safety training. Specifically, grants are awarded on a competitive basis to provide employees with training on the recognition and prevention of safety/health hazards in the workplace. The intent of the program is to reach audiences who might not otherwise receive safety training. OSHA renamed the program the Susan Harwood Training Grant Program, in 1997.
Grant applications in the past have typically fallen into three categories:
Capacity Building: OSHA awards these grants to help an organization grow or build its capacity to provide safety and health training to target audiences; small business employees, hard-to-reach or low-literacy workers, and workers in vulnerable and high-hazard industries.
Targeted Topic: These grants focus on occupational safety and health hazards associated with one of the OSHA selected training topics.
Training Materials Development: Grantees develop training materials on one of the OSHA selected training topics.
Although state or local government agencies are not eligible to apply, nonprofit organizations, including qualifying community and faith-based organizations, employer associations, and labor unions may submit applications.
The Harwood solicitation for grant applications can be found on the government-wide Grants.gov website.
CAL/OSHA Emergency Rule Adopted for Wildfire Smoke
Author, Drew Garcia, Vice President, Landscape Group, Rancho Mesa Insurance Services, Inc.
Author, Steve Hamilton, Loss Control Supervisor, Berkshire Hathaway Homestate Companies.
On Thursday, July 17 2019, the California Occupational Safety & Health Standards Board voted to adopt an emergency standard requiring employers to take action when air quality particulate matter measures greater than 150 and when there is reasonable expectation that employees will come in to contact with wildfire smoke.
Author, Drew Garcia, Vice President, Landscape Group, Rancho Mesa Insurance Services, Inc.
Author, Steve Hamilton, Loss Control Supervisor, Berkshire Hathaway Homestate Companies.
On Thursday, July 17 2019, the California Occupational Safety & Health Standards Board voted to adopt an emergency standard requiring employers to take action when air quality particulate matter measures greater than 150 and when there is reasonable expectation that employees will come in to contact with wildfire smoke.
While this may seem new to many employers, it is technically an extension of regulations currently in place including the respiratory protection standards for employees and the need to address identified hazards in the workplace. As an employer it is critical that you follow the hierarchy of controls to ensure your employees’ safety in the field. If possible, eliminate the hazard by shutting down the workforce for the day. Employees should remain indoors until particulate levels fall to acceptable. If this is not possible, try to limit the workday by rotating employees who must work outdoors, remaining cognizant of the hazards in the air and allowing employee’s time to recover in appropriate indoor areas. If neither of these options are possible, consider providing N95 respiratory protection masks.
Please remember that any type of respiratory protection provided to employees must also be accompanied by applicable training, pulmonary exams, communication on proper usage/storage and others. Links to the applicable programs can be found at this address along with sites to help you monitor air quality: https://www.dir.ca.gov/dosh/Worker-Health-and-Safety-in-Wildfire-Regions.html
This site has additional training resources in English and Spanish, handouts on proper usage of N95 masks and the history of the standard as it has been submitted. Cal/OSHA wants you to have the resources you need to effectively address the risk potential.
At this point, the regulation is on its way to the Office of Administrative Law for approval and if deemed compliant, it will go into effect 10 days after it is received. This would mean the regulation could go into effect before August.
An advisory committee will meet August 27, 2019 to begin work on a permanent version of the regulation.
If you have any questions about ways to enhance regulatory compliance, please reach out to your local resources including your insurance agent, workers’ compensation insurance safety professionals, and Cal/OSHA Consultation.
RM365 Safety Star Program May Lower Risk of Receiving OSHA’s Most Frequently Cited Violation
Author, Kevin Howard, CRIS, Account Executive, Rancho Mesa Insurance Services, Inc.
Rancho Mesa Insurance Services’ RM365 Advantage Safety Star Program™ checks several boxes for contractors who are looking to improve their safety culture and lower risk. The program provides safety training designed to reduce an organization’s probability of work-related injuries; thus, minimizing the likelihood of an OSHA citation when used in conjunction with the Risk Management Center tools.
Author, Kevin Howard, CRIS, Account Executive, Rancho Mesa Insurance Services, Inc.
Rancho Mesa Insurance Services’ RM365 Advantage Safety Star Program™ checks several boxes for contractors who are looking to improve their safety culture and lower risk. The program provides safety training designed to reduce an organization’s probability of work-related injuries; thus, minimizing the likelihood of an OSHA citation when used in conjunction with the Risk Management Center tools.
Encouraging a safety culture through proper training makes sense for employers. Fed OSHA’s, maximum fine for a non-serious violation is $12,600. A willful repeat violation, however, can cost an employer anywhere from $70,000 - $126,000.
According to the United States Department of Labor, the top 10 most frequently cited standards are:
Fall protection, construction
Hazard communication standard, general industry
Scaffolding, general requirements, construction
Respiratory protection
Control of hazardous energy (lockout/tagout), general
Ladders, construction
Powered industrial trucks, general industry
Fall Protection–Training Requirements
Machinery and Machine Guarding, general requirements
Eye and Face Protection
Avoiding OSHA’s #1 Violation
With Fall Protection being at the top of OSHA’s citation list, and one of the most frequent causes of workplace fatalities in construction, it is of the upmost importance to focus on it when developing a safety program.
Rancho Mesa’s Risk Management Center offers a number of safety trainings that cover all 10 of the most frequently cited standards listed above. Fall Protection is one of five modules, within the RM365 Advantage Safety Star Program that could potentially help avoid a severe injury and OSHA fines.
When Century Painting’s Eddie Lopez was asked to give his thoughts on becoming RM365 Safety Star certified, his response was sincere.
“Obtaining my RM365 Safety Star Certificate was not only fulfilling and educational as a safety manager, but it also helped me navigate through safety criteria that OSHA is expecting us to follow regardless,” said Eddie Lopez, Safety Manager for Century Painting Corp.
RM365 Advantage Safety Star Program™ is a comprehensive tool for contractors that are hoping to package several advantages into one single task. To learn more about how to enroll, please visit the Safety Star Program™ page or contact Rancho Mesa Insurance Services at (619) 937-0164.
To learn more about the Fall Protection in Construction requirements, visit Cal OSHA’s Safety & Health Fact Sheet. You will notice links dedicated to each industry down the left side of the page. This information can further help companies avoid a potential OSHA fine, and more importantly, protect employees.
Stay Off OSHA's Radar with an Effective Ladder Safety Program
Author, Casey Craig, Account Executive, Construction Group, Rancho Mesa Insurance Services, Inc.
Year after year OSHA publishes the “Top 10 Most Cited Violations” and it always seems to include violations dealing with falls. Fall protection, scaffolding, ladders, and fall protection (training requirements) all made this list and all of them have been on this list perennially for over a decade. How can a company that is using ladders keep from becoming just another name on the list of violators? How can you ensure that your employees are using provided equipment properly?
Author, Casey Craig, Account Executive, Construction Group, Rancho Mesa Insurance Services, Inc.
Year after year OSHA publishes the “Top 10 Most Cited Violations” and it always seems to include violations dealing with falls. Fall protection, scaffolding, ladders, and fall protection (training requirements) all made this list and all of them have been on this list perennially for over a decade. How can a company that is using ladders keep from becoming just another name on the list of violators? How can you ensure that your employees are using provided equipment properly?
The biggest mistake made with work at height is letting your employees perform their work using materials that are not meant for that job. Employees finding a chair, bucket, or truck to stand on to get those couple extra feet are the easiest ways to lead to an accident. From A-frames to extensions and step stools, there is a perfect tool for the job at hand. It does take a little preparation before sending your employees onto the job site. Having your supervisors make sure ladders are properly set up and fully functional to ensure your employees safety is as important as training your employees how to use a ladder.
Ladders have not miraculously become safer over the years. The materials used in making ladders may have changed, but the injuries that occur from using them have been the same. Here are some common misuses:
Trying to overextend reach at the top of a ladder, instead of taking the time to get all the way to the bottom to move the ladder and maintain three points of contact.
Stepping off from the third rung instead of keeping three points of contact all the way to the ground.
Setting the ladder at the wrong angle before climbing (70-75 degrees is desirable).
Trying to move a 70 pound ladder without asking for help and losing control.
There are countless ways that rushing or not paying attention to detail can leads to injuries. The American Ladder Institute (ALI) claims all injuries that occur on a ladder are preventable with the proper attention to detail. If you know that a ladder has a bent rung, or the frame is compromised, the risk is not worth having an employee get on that ladder. Ladders are manufactured to withhold four times the weight they are rated for, but if damaged there is no telling what could make it catastrophically defective. Make sure that there is enough tread on the foot of the ladder to keep your ladder in place while working at height.
Now that we know a little about our exposure, let’s see what we can do to fix the problem. Making sure you have the right equipment is by far the most important step to keep you from running into a violation. Keep your employees trained in proper ladder safety, and only let the employees that have been trained on a ladder. Properly tie off ladders, maintain your equipment over time, and attend ladder safety seminars regularly. One huge tool that is underutilized in the construction industry is having a consultation meeting with OSHA. Have them come out and inform you of things you could be doing better without the worry of being fined. OSHA is meant to be a tool to keep your employees safe, don’t hesitate to use them.
For questions about ladder safety seminars or what policies may match your company’s risk, please contact Rancho Mesa Insurance Services, Inc. at (619) 937-0164. We look forward to helping better your risk profile.
OSHA Amends Electronic Submission Requirements to Exclude Forms 300 & 301
Author, Lauren Stumpf, Media Communications Assistant, Rancho Mesa Insurance Services, Inc.
OSHA published a final rule through the Federal Register on January 25, 2019 stating, “To protect worker privacy, the Occupational Safety and Health Administration (OSHA) is amending the recordkeeping regulation by rescinding the requirement for establishments with 250 or more employees to electronically submit information from OSHA Forms 300 and 301.”
Author, Lauren Stumpf, Media Communications Assistant, Rancho Mesa Insurance Services, Inc.
OSHA published a final rule through the Federal Register on January 25, 2019 stating, “To protect worker privacy, the Occupational Safety and Health Administration (OSHA) is amending the recordkeeping regulation by rescinding the requirement for establishments with 250 or more employees to electronically submit information from OSHA Forms 300 and 301.”
All establishments with 250 or more employees, unless specifically exempted by section 14300.2 of title 8 of the California Code of Regulations, and establishments with 20 to 249 employees in the specific industries listed in Appendix H of Cal/OSHA's emergency regulations are still required to electronically submit the OSHA Form 300A (Summary of Work-Related Injuries and Illnesses).
The requirement to keep and maintain OSHA Forms 300, 300A, and 301 for five years is not changed by this final rule. This final rule becomes effective on February 25, 2019.
The deadline to electrically submit the 2018 Form 300A is March 2, 2019.
Rancho Mesa has put together a 6-minute tutorial video on how to generate the electronic Form 300A data file from the Risk Management Center, that can be uploaded to the ITA website for reporting the data.
For questions about how to track the injury and illness data in the Risk Management Center, contact Alyssa Burley at (619) 438-6869.
Sources:
https://www.osha.gov/recordkeeping/
https://www.dir.ca.gov/dosh/calosha-updates/log300-reporting.html
https://www.federalregister.gov/documents/2019/01/25/2019-00101/tracking-of-workplace-injuries-and-illnesses
Reporting Serious Workers’ Compensation Injuries
Author, Jim Malone, Workers’ CompensationClaims Advocate, Rancho Mesa Insurance Services, Inc.
Workers’ Compensation injuries occur every day. The majority of these injuries are minor incidents which require no medical treatment or loss of time from work. For others, the injury is reported to the insurance carrier, the injury is addressed, forms are provided, and the recovery from the injury is monitored until the employee is released back to work and a discharge from care is provided.
Author, Jim Malone, Workers’ CompensationClaims Advocate, Rancho Mesa Insurance Services, Inc.
Workers’ Compensation injuries occur every day. The majority of these injuries are minor incidents which require no medical treatment or loss of time from work. For others, the injury is reported to the insurance carrier, the injury is addressed, forms are provided, and the recovery from the injury is monitored until the employee is released back to work and a discharge from care is provided.
However, serious injuries, illnesses or even deaths occasionally occur at work because of a work related accident. These incidents usually require 911 calls, hospitalizations, emergency surgeries, family contact, and a longer road to recovery. They may also require immediate (within 8-24 hours) reporting to the California Occupational Safety and Health Administration (Cal/OSHA), if they meet the criterion that has been established.
As defined in the California Code of Regulations Title 8 §330(h), serious injury or illness means any injury or illness occurring in a place of employment, or in connection with any employment that:
Requires inpatient hospitalization for a period in excess of 24 hours for other than medical observation.
Results in a loss of any member of the body.
Results in a serious degree of permanent disfigurement.
Results in the death of the employee.
Does not include any injury, illness, or death caused by the commission of a Penal Code violation, except the violation of Section 385 of the Penal Code, or an accident on a public street or highway.
The California Code of Regulations Title 8 §342(a) states, “every employer shall report immediately by telephone or telegraph to the nearest District Office of the Division of Occupational Safety & Health any serious injury or illness, or death, of an employee occurring in a place of employment or in connection with any employment. Immediate means as soon as practically possible but not longer than 8 hours after the employer knows or with diligent inquiry would have known of the serious injury or illness. If the employer can demonstrate that exigent circumstances exist, the time frame for the report may be made no longer than 24 hours after the incident.”
The 8-24 hour time frame begins when the employer knows, or “with diligent inquiry” would have known of the serious injury, illness, or death. The “employer” means someone in a management or supervisory capacity.
As with any injury or accident, it can be a difficult and confusing time for all those involved and affected. It may seem like many things need to be done all at once. That is, of course, impossible. So, prepare yourself now. Make a list of your responsibilities and important contact numbers before a serious injury or accident occurs.
The order in which you perform each of these responsibilities may differ, according to the type of injury or accident that occurs. However, you will still have your checklist and contact numbers ready to use to ensure you do not forget any particular step or obligation. This emergency list of telephone numbers may be your broker, safety/loss control specialist, claims administrator, or workers’ compensation claims advocate. We are all available to provide you with any assistance you may need.
For those in California, the Cal/OSHA District Office contact list is below. Ask for the officer of the day.
Concord (925) 602-6517
Oakland (510) 622-2916
San Francisco (415) 972-8670
Cal/OSHA Link: www.dir.ca.gov/title8/342.html
For additional information, please contact Rancho Mesa Insurance Services, Inc. at (619) 937-0164.
Developing an Effective Injury and Illness Prevention Program (IIPP)
Author, Daniel Frazee, Executive Vice President, Rancho Mesa Insurance Services, Inc.
If you have operated a business in the state of California for any period of time, you have very likely heard about or run across the acronym IIPP. Wherever you stand with your knowledge within the world of safety, injury, and illness, it is important for every organization to understand the mandatory parts of an IIPP. What is often overlooked is how developing an effective safety program can create positive change and truly impact your bottom line.
Author, Daniel Frazee, Executive Vice President, Rancho Mesa Insurance Services, Inc.
If you have operated a business in the state of California for any period of time, you have very likely heard about or run across the acronym IIPP. Wherever you stand with your knowledge within the world of safety, injury, and illness, it is important for every organization to understand the mandatory parts of an IIPP. What is often overlooked is how developing an effective safety program can create positive change and truly impact your bottom line.
What is an IIPP?
An Injury and Illness Prevention Program (IIPP) is a required written workplace safety document that must be maintained by California employers (Title 8 of the CA code of regulations, section 3203). These regulations require eight (8) specific elements that are summarized below. In many cases, this process requires direct questions about how the company currently views and manages safety. Answering these questions will begin to highlight the positive aspects of what already is currently in place and shed light on areas that need improvement.
Responsibility
Clarifying the name, title and contact information for the person(s) with overall responsibility for the IIPP is a critical first step to this process. Making the IIPP available and accessible at all business locations becomes the first task of the “responsible person.”
Compliance
What is the content of the company’s safety meetings? Who runs those meetings? How do you discipline employees if they do not follow safety guidelines? How might the company recognize or reward their employees for safe practices or behavior?
Communication
Safety meetings are held on what type of schedule within your organization? How can employees anonymously notify management of safety and health concerns without fear of reprisal? Is there a safety committee in place that provides communication to all employees? If not, who would be considered as important members of that committee?
Hazard Assessment
Who within the company is responsible for periodic inspections to identify and evaluate workplace hazards? Provide detail on this schedule along with accompanying documentation that these visits occurred. Continuously communicating with employees for feedback and constantly reviewing hazards on a jobsite or within the workplace are crucial. Lastly, does the company use a standard or tailored JHA (Job Hazard Analysis) checklist to accomplish this? Re-visiting these checklists regularly as exposures change is critical to reducing claim frequency.
Accident/Exposure Investigation
Post-accident, who is the name of the person within the organization responsible for conducting those investigations? What type of form or checklist are you using to establish “root causes” of the accident or injury? And, back to the compliance section, what type of discipline could be handed down in the event of employee error that causes an accident or injury?
Hazard Correction
After the company has identified the hazard and determined exactly how and why an incident occurred, the IIPP must provide detail on how the company will correct the problem from happening again. One solid first step can include a review of Personal Protective Equipment (PPE) use. That is, did the equipment being used cause the accident or injury and, if yes, why? Answering the\is question may show that the piece of equipment was not appropriate for the task, or the item was defective or too old, which caused failure.
Training and Instruction
Ongoing and job specific training and instruction are really the lifeblood of any truly effective IIPP. Presenting the information in a clear, concise format that is easily understood is often the most difficult task in this process. Yet, it remains perhaps the most important as it is vital that employees are continually educated and RETAIN their instruction. Peeling back this process with managers, foreman, superintendents, etc. and learning specifically how the training is being disseminated, allows for a true baseline to be established.
Recordkeeping
Document, document, document! While establishing a written version of the IIPP might be the first step, and revising/editing on an annual basis is recommended, having the proper documentation that accompanies each section is just as important. This provides the responsible person(s) an important tool to continually compare the company’s actions, trainings, assessments and prevention techniques with the available documentation.
Can An Effective IIPP Impact my Bottom Line?
Building an effective IIPP means that the document represents a part of the company’s culture. For it to be meaningful and have a real impact on reducing workplace injuries and illnesses, it must reflect what your company is actually doing on a day to day basis. As the company’s ownership ties this into the overall business, building the IIPP from the ground up into a living, breathing document has measurable impact on controllable costs like workers’ compensation. Reducing frequency of injury can help lower the experience modification, improve the loss ratio, and establish a solid risk profile in the insurance marketplace. Having the supporting documentation along with specific examples of forms, checklists and assessments can arm an insurance broker with the tools they need in the marketplace. More specifically, this information provides a broker important leverage points when negotiating the most competitive terms possible for the employer with the insurance carrier’s underwriter. Those points can lead directly to premium savings, which leads to healthier margins and stronger profitability. Build the IIPP because it is a CA state requirement and it is the right thing to do. But, believe that building a first class safety program will absolutely lower your long-term insurance costs.
For a sample IIPP, visit the Risk Management Center or contact Alyssa Burley at (619) 438-6869.
Cal/OSHA Issues Electronic Filing Requirement For 2017 OSHA 300A Form
Author, Alyssa Burley, Client Services Coordinator, Rancho Mesa Insurance Services, Inc.
In April 2018, federal OSHA announced all affected employers are required to submit injury and illness data (i.e., Form 300A data) via the Injury Tracking Application (ITA) online portal by July 1, 2018, even if the employer is covered by a state plan like those in California, Maryland, Minnesota, South Carolina, Utah, Washington or Wyoming.
Author, Alyssa Burley, Client Services Coordinator, Rancho Mesa Insurance Services, Inc.
In April 2018, federal OSHA announced all affected employers are required to submit injury and illness data (i.e., Form 300A data) via the Injury Tracking Application (ITA) online portal by July 1, 2018, even if the employer is covered by a state plan like those in California, Maryland, Minnesota, South Carolina, Utah, Washington or Wyoming.
Cal/OSHA then issued a statement in May 2018, advising affected employers “to comply with federal OSHA’s directive to provide Form 300A data covering calendar year 2017," even though it was not a Cal/OSHA requirement.
“On November 1, 2018,” according to the Cal/OSHA website, “the Office of Administrative Law approved the emergency action. This means that the employers in California described below are now required to submit Form 300A data covering calendar year 2017 by December 31, 2018. These employers should follow the instructions posted at federal OSHA's ITA website:
Check Appendix H for your industry. It includes industries like: Construction; Community/Nursing/Residential Care facilities; Community Food/Housing Relief Services; and many more.
All employers with 250 or more employees, unless specifically exempted by section 14300.2 of title 8 of the California Code of Regulations
Employers with 20 to 249 employees in the specific industries listed in Appendix H of the emergency regulations.”
This emergency action by the Office of Administrative Law brings Cal/OSHA’s requirements up to the federal OSHA’s minimum standards, with one difference. Federal OSHA required affected employers covered by state plans to submit the 2017 Form 300A data electronically by July 1, 2018, while this new action requires affected California employers to submit the data by December 31, 2018.
Since the Federal OSHA deadline has already passed, it is recommended that all affected employers in California who have not already submitted the 2017 Form 300A data via the ITA, submit it as soon as possible, but no later than December 31, 2018.
Next year, the deadline for electronically submitting 2018 Form 300A data will be March 2, 2019.
Rancho Mesa has put together a 9-minute tutorial video on how to generate the electronic Form 300A data file from the Risk Management Center, that can be uploaded to the ITA website for reporting the data.
For questions about how to track the injury and illness data in the Risk Management Center, contact Alyssa Burley at (619) 438-6869.
Key Steps to Take Before, During, and After an OSHA Inspection
Author, Sam Clayton, Vice President, Construction Group, Rancho Mesa Insurance Services, Inc.
An OSHA officer can show up to your facility or worksite for any number of reasons: employee complaints, accidents, programmed inspections, sweeps, follow-up or a drive-by observation. In order to ensure a smooth inspection, we suggest you prepare before OSHA appears at your door. Here are some key steps to take before, during and after an OSHA inspection.
Author, Sam Clayton, Vice President, Construction Group, Rancho Mesa Insurance Services, Inc.
An OSHA officer can show up to your facility or worksite for any number of reasons: employee complaints, accidents, programmed inspections, sweeps, follow-up or a drive-by observation. In order to ensure a smooth inspection, we suggest you prepare before OSHA appears at your door. Here are some key steps to take before, during and after an OSHA inspection.
Before the Inspection
Every company should have a formal plan in place detailing what should be done before, during and after an OSHA inspection. This procedure should be site specific and available to all supervisors. Site specific information should include company contacts for the project if OSHA arrives, location of documents like OSHA 300 logs and the Injury and Illness Prevention Program (IIPP).
Upon arrival of the OSHA inspection officer, the company should verify the officer’s credentials and try to determine why they are at the site. Before the opening conference begins, the employer should assign specific individuals to be the note taker and the photographer. It is also extremely important to remind everyone involved to be professional and treat the compliance officer with respect.
During the Inspection
Opening Conference: During the opening conference, you will want to establish the scope of the inspection, the reason for the inspection, and the protocol for any employee interviews or production of documents. If the inspection is triggered by an employee complaint, the employer may request a copy.
Physical Inspection: During the inspection, the OSHA compliance officer will conduct a tour of the worksite or facility in question to inspect for safety hazards. It is likely pictures will be taken by the compliance officer. Instruct your photographer to also take the same pictures and possibly additional pictures from different angels while the note taker should take detailed notes of the findings.
Closing Conference: At the closing conference, the OSHA compliance officer typically will explain any citations, the applicable OSHA standards and potential abatement actions and deadlines. It is important that during this process the company representative takes detailed notes and asks for explanations regarding any violations. If any of the alleged violations have been corrected, you will want to inform the OSHA compliance officer.
After the Inspection
If you are told no citations will be issued, contact the compliance officer and obtain a Notice of No Violation after Inspection (Cal/OSHA 1 AX). If you receive a citation, it is important to take immediate action because a company only has 15 working days after the inspection to notify the Appeals Board, if they choose to appeal the citation. Citations can be issued up to six months after the inspection, so it is important to watch your mail closely during this time.
For a proactive approach to OSHA inspections, contact the Consultation Services Branch for your state (i.e. Cal/OSHA) or Federal OSHA Consultation. They will be able to provide consultative assistance to you through on-site visits, phone support, educational materials and outreach, and partnership programs.
Register for the "How to Survive an OSHA Visit" webinar hosted by KPA on Monday, June 25, 2018 from 11:00 am - 12:00 pm PST to learn about what OSHA looks for during an inspection.
For additional information, please contact Rancho Mesa Insurance Services, Inc. at (619) 937-0164.
Risk Management Center Streamlines Electronic OSHA Reporting
Author, Alyssa Burley, Client Services Coordinator, Rancho Mesa Insurance Services, Inc.
The Occupational Health and Safety Administration (OSHA) now require certain employers to electronically submit their completed 2016 Form 300A. OSHA has created a website that allows employers to manually complete the information or upload a formatted CSV (comma-separated values) file
Author, Alyssa Burley, Client Services Coordinator, Rancho Mesa Insurance Services, Inc.
Editor's Note: This post was originally published on November 9, 2017 and has been updated to reflect the latest available information.
The Occupational Health and Safety Administration (OSHA) now requires certain employers to electronically submit their completed Form 300A. OSHA has created a website that allows employers to manually complete the information or upload a formatted CSV (comma-separated values) file. Users of Rancho Mesa’s Risk Management Center have the ability to track incidents and generate the export file, making the electronic reporting process quick and simple.
Check federal OSHA or your state's OSHA website for specific filing date deadlines.
Prepare and Submit
Once an incident occurs, Risk Management Center users track the details within the online system. All of the required information is stored and made available through reports and an export.
Request a Risk Management Center Account.
To export the OSHA 300A Report data, login to the Risk Management Center. Then, navigate to the Applications list and click on Incident Track®.
From this screen, click on the Reports menu and click the Export Data option.
Choose the report, “OSHA 300A Report” and select the export type a CSV. Choose the year and either all your sites or just one. Click the Export button and enter your email address.
The .CSV file will be generated and emailed to you. Save the file on your computer so it can be uploaded to OSHA’s Injury Tracking Application (ITA).
To upload the .CSV file, login to OSHA’s ITA and follow the instructions on the screen.
Who is Required to Submit?
According to OSHA, “establishments with 250 or more employees are currently required to keep OSHA injury and illness records and establishments that are classified in certain industries with historically high rates of occupational injuries and illnesses.” Some of those industries include construction, manufacturing, health and residential care facilities, and building services.
On April 30, 2018, OSHA announced State Plans have been informed “that for Calendar Year 2017 all employers covered by State Plans will be expected to comply. An employer covered by a State Plan that has not completed adoption of a state rule must provide Form 300A data for Calendar Year 2017. Employers are required to submit their data by July 1, 2018. There will be no retroactive requirement for employers covered by State Plans that have not completed adoption of their own state rule.
Cal/OSHA released a statement explaining that "even though California has not yet adopted its own state rule, employers are advised to comply with federal OSHA's directive to provide Form 300A data covering calendar year 2017." In addition, other states like Maryland, Minnesota, South Carolina, Utah, Washington and Wyoming may follow California's lead.
For questions about tracking and exporting OSHA reports with the Risk Management Center, contact Rancho Mesa at (619) 937-0164
Federal OSHA Asserts Electronic Data Reporting Requirement Applies to Employers Across All States
Author, Alyssa Burley, Client Services Coordinator, Rancho Mesa Insurance Services, Inc.
The federal Occupational Safety and Health Administration (OSHA) announced Monday, April 30, 2018 it has “taken action to correct an error that was made with regard to implementing the final rule” which required some employers to electronically submit their injuring and illness reports via the Injury Tracking Application (ITA) online.
Author, Alyssa Burley, Client Services Coordinator, Rancho Mesa Insurance Services, Inc.
The federal Occupational Safety and Health Administration (OSHA) announced Monday, April 30, 2018 it has “taken action to correct an error that was made with regard to implementing the final rule” which required some employers to electronically submit their injuring and illness reports via the Injury Tracking Application (ITA) online.
Federal OSHA has determined that Section 18(c)(7) of the Occupational Safety and Health Act requires employers in State-administered OSHA plans “to make reports to the Secretary in the same manner and to the same extent as if the plan were not in effect.” Therefore, federal OSHA’s statement asserts “employers must submit injury and illness data in the Injury Tracking Application (ITA) online portal, even if the employer is covered by a State Plan that has not completed adoption of their own state rule.”
According to the announcement, State Plans have been informed “that for Calendar Year 2017 all employers covered by State Plans will be expected to comply. An employer covered by a State Plan that has not completed adoption of a state rule must provide Form 300A data for Calendar Year 2017. Employers are required to submit their data by July 1, 2018. There will be no retroactive requirement for employers covered by State Plans that have not completed adoption of their own state rule.”
“Even though California has not yet adopted its own state rule, employers are advised to comply with federal OSHA’s directive to provide Form 300A data covering calendar year 2017.”
This announcement comes on the heels of a March 2018 report by Bloomberg Environment that indicated federal OSHA anticipated more than 350,000 worksites to submit Form 300A reports via the online portal, yet nearly 200,000 weren’t submitted by the December 31, 2017 deadline. That means only 153,653 Form 300A reports were submitted and another 60,992 worksites submitted reports that were not required.
In May 2017, Cal/OSHA published a statement indicating “California employers are not required to follow the new requirements and will not be required to do so until ‘substantially similar’ regulations go through formal rulemaking, which would culminate in adoption by the Director of the Department of Industrial Relations and approval by the Office of Administrative Law." However, with the recent announcement from federal OSHA, Cal/OSHA released a statement explaining that "even though California has not yet adopted its own state rule, employers are advised to comply with federal OSHA's directive to provide Form 300A data covering calendar year 2017." In addition, other states like Maryland, Minnesota, South Carolina, Utah, Washington and Wyoming may follow California's lead.
Rancho Mesa’s Incident Track® is an effective way to manage incidents and maintain required OSHA logs. As just one of the many “tracks” inside the Agency’s “Risk Management Center,” Incident Track can also generate electronic report files that can be uploaded into the Federal OSHA’s ITA online portal.
Contact Alyssa Burley with follow up questions about these OSHA requirements and/or an interest in learning more about tracking incidents through our client based portal.
Workplace Violence Insurance Surges in Aftermath of Shootings
Author, Sam Brown, Vice President, Human Services Group, Rancho Mesa Insurance Services, Inc.
In response to the hundreds of mass shootings taking place each year, the insurance marketplace has produced new workplace violence products to help employers and employees recover from a crisis.
Author, Sam Brown, Vice President, Human Services Group, Rancho Mesa Insurance Services, Inc.
In response to the hundreds of mass shootings taking place each year, the insurance marketplace has produced new workplace violence products to help employers and employees recover from a crisis.
U.S. employers have an obligation for duty of care for the safety, health, and security of employees (see Occupational Safety and Health Administration (OSHA) Act of 1970). Duty of care requires protection against workplace violence hazards.
A mass shooting is an attack resulting in 4 or more.
Year | # of Incidents |
---|---|
2017 | 327 |
2016 | 385 |
2015 | 333 |
It is the employer's obligation to protect its employees from violence. Homeland Security defines an active shooter as “an individual actively engaged in killing or attempting to kill people in a confined and populated area.” While OSHA describes workplace violence as “any act or threat of physical violence, harassment, intimidation, or other threatening disruptive behavior that occurs at the work site.” What is your organization doing to protect its people from these types of events?
Over the last three years, the United States recorded an average of 348 mass shootings per year.
Description | Cost |
---|---|
Support for survivors and families of victims | $2.7 million |
Cleanup, renovations, and other facility changes | $6.4 million |
Settlement payments and other legal costs | $4.8 million |
Costs to Consider
As victims, families, and co-workers struggle to heal after losing friends and loved ones, the costs continue to mount.
Aside from treating survivors, consider some of the costs from the Virginia Tech University shooting: survivor support, cleanup, renovations, facility changes, settlement payouts and legal costs.
How would your organization absorb the cost of such an event?
Workplace Violence Policy Coverage
In addition to providing a consultant to guide businesses through an emergency event, a covered event will trigger legal liability coverage to address legal expenses. These expenses may be related to the following:
- Business interruption expense
- Defense and indemnity expenses
- Public relations counsel
- Psychiatric care
- Medical or dental care
- Employee counseling
- Temporary security measures
- Rehabilitation expenses
- Limits start at $1,000,000 with $0 deductible
Among other underwriting considerations, when pricing workplace violence policies, carriers factor in operations like exchanging money with the public, working with volatile or unstable people, providing services and care to the public, and working where alcohol is served. Take a look at your organization's operations to see if there is a risk.
Please contact Rancho Mesa Insurance Services to discuss whether this insurance is right for your organization.
Information sourced from McGowan Program Administrators.
Simple Steps to Developing a Personal Protective Equipment Program
Author, Jeremy Hoolihan, Account Executive, Rancho Mesa Insurance Services, Inc.
In the workplace, employees can be exposed to potentially harmful hazards. Identifying these hazards and using precautionary measures such as personal protective equipment (PPE) can mean the difference between a safe jobsite and an injury.
Author, Jeremy Hoolihan, Account Executive, Rancho Mesa Insurance Services, Inc.
In the workplace, employees can be exposed to potentially harmful hazards. Identifying these hazards and using precautionary measures such as personal protective equipment (PPE) can mean the difference between a safe jobsite and an injury.
PPE “is equipment worn to minimize exposure to a variety of hazards,” according to the Occupational Safety and Health Administration’s (OSHA) booklet on the subject. Examples of PPE include gloves, foot and eye protection, earplugs, hard hats, respirators and full body suites.
Implementing a PPE program can greatly reduce the chances of workplace injuries and increase a business’s productivity.
A PPE Program consists of three main components:
- An assessment of the workplace hazards and procedures, and determining what PPE will be used to protect employees.
- Employee training.
- Documentation of hazard assessment and employee training.
Conducting a Hazard Assessment
The OSHA Personal Protective Equipment Standard (29 CFR 1910.132-138) requires that employers ensure appropriate PPE is “provided, used, and maintained in a sanitary and reliable condition whenever it is necessary” to protect workers from hazards. Employers are required to assess the workplace to determine if hazards that require the use of personal protective equipment are present or are likely to be present. The following information will aid in the hazard assessment process:
- Develop a Hazard Assessment Checklist (a sample is available in the Risk Management Center) to identify exposures in the workplace that could injure a specific body part such as eyes, face, hand, arms, feet, legs, body, head, or hearing. Once you have identified the potential exposures, include the required PPE to minimize or eliminate the exposure.
- Conduct a walk-through survey of the workplace and complete the information on the Hazard Assessment Checklist. The purpose of the survey is to identify sources of hazards to workers such as chemical exposures, harmful dust, sharp objects, electrical hazards, etc.
- Select suitable PPE. Should an employer determine that PPE is necessary, they are then required to ensure that it is available and used. It is not enough to select PPE and witness its use, however. Employers must also make sure that the PPE is suitable for protection from the identified hazards, is properly fitted, and is not defective or damaged in any way.
Employee Training
Before doing work which requires PPE, employees must be trained to know the following:
- When PPE is necessary.
- The type of PPE that is necessary.
- How the PPE is properly worn.
- PPE's limitations.
- How to properly care, maintain, and disposal of the PPE.
Written Verification of Hazard Assessments and Employee Training
Employers are responsible for ensuring that employees are trained in the use of PPE and must provide written certification to that effect. Employers must also certify in writing that the employees understand the training. Also, in general, employers must provide required PPE at no cost to employees.
A large majority of workplace injuries are preventable through the implementation of a PPE Program. It is the employer’s responsibility to keep their employees adequately protected at all times. After all, it is certainly difficult to imagine a firefighter performing his or her duties without a helmet, boots, gloves and other necessary protective equipment.
Rancho Mesa Insurance Services has expertise in risk management for the construction industry. We can provide you with assistance in developing a PPE Program, as well as other risk management and insurance needs. Please contact me with any questions at (619) 937-0174 or jhoolihan@ranchomesa.com.
Reminder: 2017 OSHA Summary of Work-Related Injuries and Illness Must Be Posted
Author, Alyssa Burley, Client Services Coordinator, Rancho Mesa Insurance Services, Inc.
According to a recent memo, the State of California Department of Industrial Relations would like to remind employers that they are required to physically post their 2017 annual summaries of work-related injuries from February 1, 2018 through April 30, 2018.
Author, Alyssa Burley, Client Services Coordinator, Rancho Mesa Insurance Services, Inc.
According to a recent memo, the State of California Department of Industrial Relations would like to remind employers that they are required to physically post their 2017 annual summaries of work-related injuries from February 1, 2018 through April 30, 2018.
OSHA’s Summary of Work-Related Injuries and Illness, also known as Form 300A, must be completed and posted for employees to view.
If you are tracking work-related injuries in the Rancho Mesa Risk Management Center, the Form 300A can be generated from the system. From the Incident Track screen, click on "Reports," then "OSHA Reports," select "OSHA 300A Summary," the "2017." Complete any missing information and "Download."
To manually complete the Form 300A, review the instructions found on the Cal/OSHA or OSHA websites.
If you are unsure if you are required to maintain OSHA logs, visit the OSHA website.
Building an Effective Fall Protection Program
Author, Daniel Frazee, Executive Vice President, Rancho Mesa Insurance Services, Inc.
In a Census summarizing fatal occupational injuries from 2016, those originating from falls continued a steady upward trend that began in 2011 and increased another 6% in 2016. More specifically, falls increased more than 25% for roofers, painters, carpenters, tree trimmers & pruners. Since 2013, fall protection citations have been #1 or #2 on OSHA’s most cited violations. Now, more than ever, it is essential for employers with personnel who work at heights to provide comprehensive fall protection.
Author, Daniel Frazee, Executive Vice President, Rancho Mesa Insurance Services, Inc.
In a Census, summarizing fatal occupational injuries from 2016, those originating from falls continued a steady upward trend that began in 2011 and increased another 6% in 2016. More specifically, falls increased more than 25% for roofers, painters, carpenters, tree trimmers & pruners. Since 2013, fall protection citations have been #1 or #2 on OSHA’s most cited violations. Now, more than ever, it is essential for employers with personnel who work at heights to provide comprehensive fall protection.
Job Hazard Analysis
While developing any type of new safety program, experts encourage breaking the process into steps. These steps must be designed for all construction sites where exposure to height exists. And the plan must be prepared by a competent (qualified) person, defined as someone with extensive knowledge and training on fall protection systems. The initial step requires a job hazard analysis to be performed at the location in advance of work commencing. The analysis can include determining the average & maximum height at which work will be performed, identifying the number of employees using the area, observing potential hazards that might compromise the work, and modifying work to reduce exposure. According to the American National Standards Institute (ANSI), “the most desirable form of protection is elimination of the need to work from height” (Z359.2, section 5.1).
Types of Fall-Arrest Systems
Assuming hazards cannot be eliminated and the need to work from height still exists, employers can implement both passive and active fall-arrest systems. Passive systems can include examples such as guardrails or ladder cages while the more technical active fall-restraint systems can use specialized lanyards and anchors to eliminate fall exposure. These require individualized training that is crucial for proper use and effectiveness.
Proper Implementation & Calculating Fall Clearance
Once you have identified the appropriate system for the jobsite, the implementation is critical to the success of the program. Using the more complex active fall-arrest system as an example, employers can track their progress with four steps:
- Anchorage-the secure point of attachment to the fall arrest system. The structure must be capable of supporting at least 5,000 pounds/worker or meet OSHA’s criteria of a 2:1 safety factor.
- Body Support-the connection point to the anchorage, commonly seen with a full body harness that distributes the forces of a fall over the chest, shoulders, pelvis & thighs.
- Connectors-examples include lanyards and self-retracting lifelines, devices that connect or link the harness to the anchorage.
- Descent & Rescue-all good fall protection programs must have a plan for rescue or retrieval of a fallen worker. Employees need to be raised or lowered to a safe location when needed.
As employers build out their fall-arrest system, calculating fall clearance and swing fall hazards represent key components to a successful program. In part, this can be achieved by determining sufficient clearance below the worker to stop the fall before he/she hits the ground or another object. It should include an awareness of the anchorage location, the connecting system, deceleration distance, the height of the suspended worker, etc.
Training, Training, Training
Formal, written training programs only become effective tools when employers combine classroom knowledge with practical, hands-on experience. Competent persons need to continually educate workers on industry regulations, proper equipment selection/use and ongoing maintenance standards. This must be emphasized on a consistent basis so that workers understand the importance of fall protection as it relates to their own safety and that of the company.
Improving Your Risk Profile
Without argument, the most important reason for introducing a Fall Protection program is the safety and well-being of your employees. Getting workers home safely at the end of every work day remains every employer’s ultimate goal. A second goal for consideration is that of improving your company’s risk profile to the insurance marketplace. If your construction firm performs work in excess of 2 stories, underwriters expect to see details on your Fall Protection program. While just one aspect of a Best Practices renewal strategy, providing a copy of your program with training examples and site specific layouts can give insurance company underwriters the comfort level they need to deliver more competitive quote proposals. Allowing your insurance broker these reference points can help them engage more options which can lead to better terms and pricing, and lower overall insurance costs for your company.
As your company builds out safety modules and looks to refresh or develop new a Fall Protection program, look to Rancho Mesa Insurance and their Risk Management Center (RMC) for assistance. The RMC contains endless content, program templates and resources for our construction partners. Additionally, the Agency’s monthly offerings of industry specific trainings and webinars provides the education our clients need to stay ahead of their competition.
For more information about fall protection, contact Rancho Mesa Insurance Services, Inc. at (619) 937-0164.
OSHA Accepting Electronic Form 300A Data Submissions Through End of Year
Author, Alyssa Burley, Client Services Coordinator, Rancho Mesa Insurance Services, Inc.
In a recent news release from the U.S. Department of Labor (DOL), the Occupational Safety and Health Administration (OSHA) will be accepting electronically submitted 2016 OSHA Form 300A data through midnight on December 31, 2017. The previous deadline had been December 15, 2017.
Author, Alyssa Burley, Client Services Coordinator, Rancho Mesa Insurance Services, Inc.
In a recent news release from the U.S. Department of Labor (DOL), the Occupational Safety and Health Administration (OSHA) will be accepting electronically submitted 2016 OSHA Form 300A data through midnight on December 31, 2017. The previous deadline had been December 15, 2017.
According to a statement released by the DOL, as of January 1, 2018, the Injury Tracking System "will no longer accept the 2016 data."
Employers in California, Maryland, Minnesota, South Carolina, Utah, Washington and Wyoming are currently not required to submit their OSHA reports electronically. However, it is likely it will be a requirement in the future.
Update: 5/3/18 For updated information on State requirements, read "Federal OSHA Asserts Electronic Data Reporting Requirement Applies to Employers across All States."
For additional information about the OSHA electronic reporting, read "Risk Management Center Streamlines Electronic OSHA Reporting," "DHS Alerts OSHA of Possible Electronic Reporting Security Breach," "OSHA Launched Electronic Reporting System."
OSHA Pushes Back Electronic Reporting Deadline
Author, Alyssa Burley, Client Services Coordinator, Rancho Mesa Insurance Services, Inc.
In a recent news release from the U.S. Department of Labor (DOL), the Occupational Safety and Health Administration (OSHA) announced it has extended its electronic reporting deadline from December 1, 2017 to December 15, 2017.
Author, Alyssa Burley, Client Services Coordinator, Rancho Mesa Insurance Services, Inc.
In a recent news release from the U.S. Department of Labor (DOL), the Occupational Safety and Health Administration (OSHA) announced it has extended its electronic reporting deadline from December 1, 2017 to December 15, 2017.
The extension was made "to allow affected employers additional time to become familiar with the new electronic reporting system launched on August 1, 2017," according to the statement issed by the DOL's OSHA.
Employers in California, Maryland, Minnesota, South Carolina, Utah, Washington and Wyoming are currently not required to submit their OSHA reports electronically. However, it is likely it will be a requirement in the future.
Update: 5/3/18 For updated information on State requirements, read "Federal OSHA Asserts Electronic Data Reporting Requirement Applies to Employers across All States."
For additional information about the OSHA electronic reporting, read "Risk Management Center Streamlines Electronic OSHA Reporting," "DHS Alerts OSHA of Possible Electronic Reporting Security Breach," "OSHA Launched Electronic Reporting System."
OSHA Announces Top 10 Cited Violations for FY 2017
Author, Sam Clayton, Vice President, Construction Group, Rancho Mesa Insurance Services, Inc.
The Occupational Safety and Health Administration (OSHA) released its preliminary top 10 citation list for fiscal year 2017 at the annual National Safety Council (NSC) Congress and Expo, held in late September 2017.
Author, Sam Clayton, Vice President, Construction Group, Rancho Mesa Insurance Services, Inc.
The Occupational Safety and Health Administration (OSHA) released its preliminary top 10 citation list for fiscal year 2017 at the annual National Safety Council (NSC) Congress and Expo, held in late September 2017.
“One thing I’ve said before in the past on this is, this list doesn’t change too much from year to year,” said Patrick Kapust, deputy director of OSHA’s Directorate of Enforcement and Programs, during the expo presentation. “These things are readily fixable. I encourage folks to use this list and look at your own workplace.”
OSHA compiled the list using data collected from incidents occurring from October 2016 through September 2017.
- Fall Protection in Construction: 6,072 violations.
Frequently violated requirements include unprotected edges and open sides in residential construction and failure to provide fall protection on low-slope roofs - Hazard Communication: 4,176 violations.
Not having a hazard communication program topped the violations, followed by not having or providing access to safety data sheets - Scaffolding: 3,288 violations.
Frequent violations include improper access to surfaces and lack of guardrails - Respiratory Protection: 3,097 violations.
Failure to establish a respiratory protections program topped these violations, followed by failure to provide medical evaluations - Lockout/Tagout: 2,877 violations.
Frequent violations were inadequate worker training and inspections not completed. - Ladders in Construction: 2,241 violations.
Frequent violations include improper use of ladders, damaged ladders and using the top step. - Powered Industrial Trucks: 2,162 violations.
Violations include inadequate worker training and refresher training. - Machine Guarding: 1,933 violations.
Exposure points of operation topped these violations. - Fall Protection-training requirements: 1,523 violations.
Common violations include failure to train workers in identifying fall hazards and proper use of fall protection equipment. - Electrical-wiring methods: 1,405 violations.
Violations of this standard were found in most general industry sectors, including food and beverage, retail and manufacturing
Training materials for each of the items on the OSHA list are available within the Risk Management Center. Contact Rancho Mesa Insurance Services, Inc. at (619) 937-0164, for more information.
Is your Company Prepared for OSHA’s new Silica Rule?
Author, Sam Clayton, Vice President, Construction Group, Rancho Mesa Insurance Services, Inc.
On September 23rd 2017 the Occupational Safety and Health Administration’s (OSHA) new silica standard for construction will go into effect. This means contractors who engage in activities that create silica dust or are known in the industry as respirable crystalline silica, must meet a stricter standard for how much dust there workers inhale.
Author, Sam Clayton, Vice President, Construction Group, Rancho Mesa Insurance Services, Inc.
On September 23rd 2017 the Occupational Safety and Health Administration’s (OSHA) new silica standard for construction will go into effect. This means contractors who engage in activities that create silica dust or are known in the industry as respirable crystalline silica, must meet a stricter standard for how much dust their workers inhale.
What is Crystalline Silica?
Crystalline silica is a common mineral that is found in material that we see every day in roads, buildings and sidewalks. It is a common component of sand, stone, rock, concrete, brick, block and mortar.
What are the Effects?
Exposures to crystalline silica dust occur in common workplace operations involving cutting, sawing, drilling, and crushing of rock, and stone products such as construction tasks and operations using sand products like in glass manufacturing, foundries, sand blasting and hydraulic fracking. Inhaling silica dust can lead to silicosis, an incurable lung disease that can be fatal. Those with too much silica exposure can also develop lung cancer, kidney disease and chronic obstructive pulmonary disease.
What is the New Standard?
The new silica rule lowers the permissible exposure limit from the current standard of 250 micrograms per cubic meter of air to 50 micrograms per cubic meter of air, averaged over an eight hour day, and an action level of 25 micrograms per cubic meter of air.
How will the New Standard protect workers?
The rule significantly reduces the amount of silica dust that workers can be exposed to on the job. That means employers will have to implement controls and work practices that reduce workers exposures to silica dust. For most activities, that means employers will have to ensure the silica dust is wet or vacuumed up before workers can work in the area. Employers are required under the rule to provide training, respiratory protection when controls are not enough to limit exposure and written exposure control plans, measure controls in some cases limit access to high exposure areas. Employers are also required to offer medical exams to highly exposed workers.
How can your company protect itself from Silica Related Claims?
In addition to implementing the necessary controls to protect your employees, we would highly recommend you review your insurance policies to make sure that your company is protected from silica related claims.
Over the last few years, we’ve seen quite a few General Liability carriers putting Silica exclusions on there policies. This isn’t always the case and may be negotiated out depending on the carrier. Another alternative is to obtain a Contractors Pollution Policy that would provide the necessary coverage for this exposure.
Rancho Mesa also recommends taking advantage of the Silica Exposure Training materials available within the Risk Management Center. These materials include an online training course, PowerPoint presentation, training short and quiz in both English and Spanish. Should you have any questions, please contact Rancho Mesa Insurance Services at 619-937-0164.