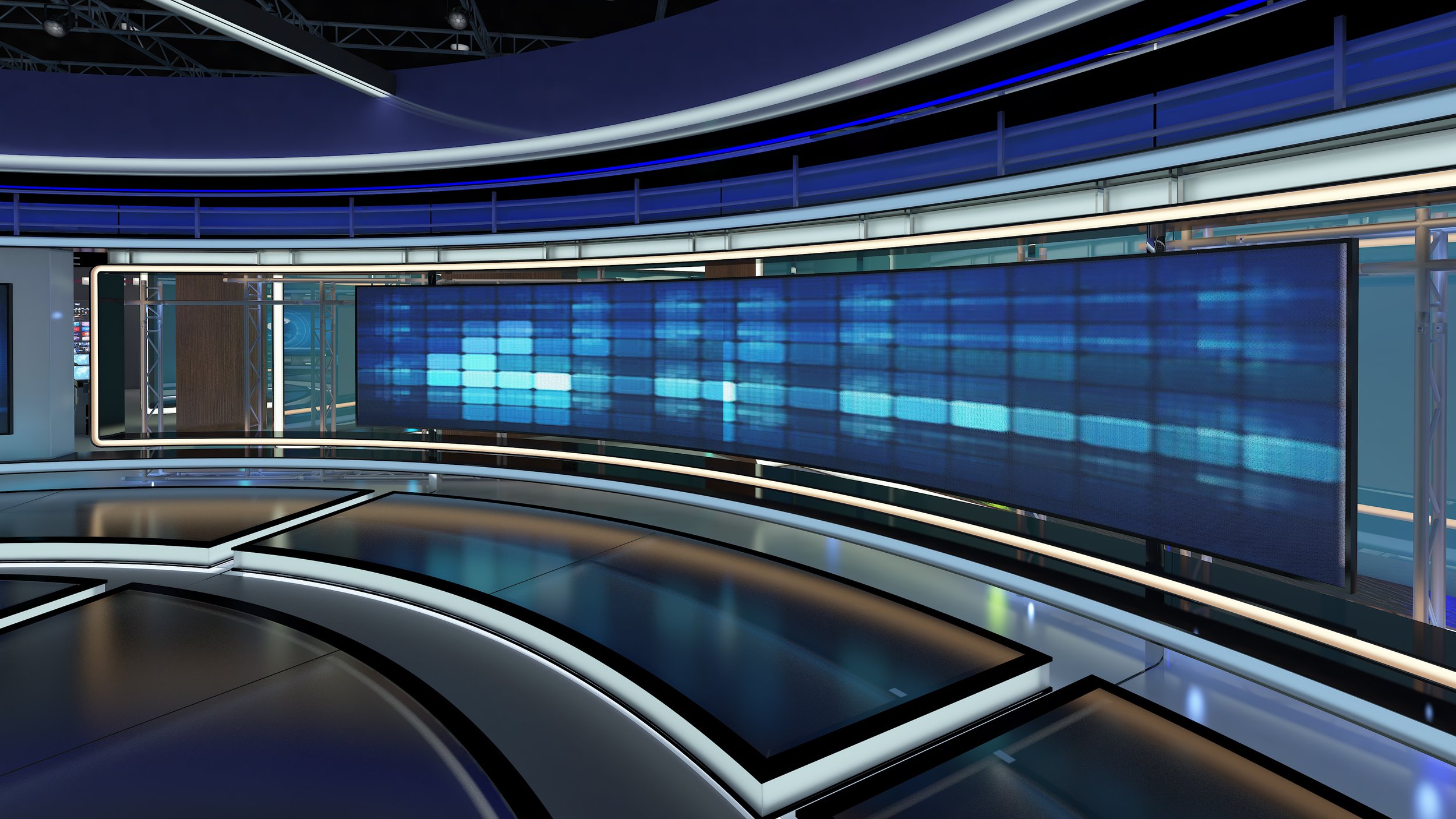
Industry News
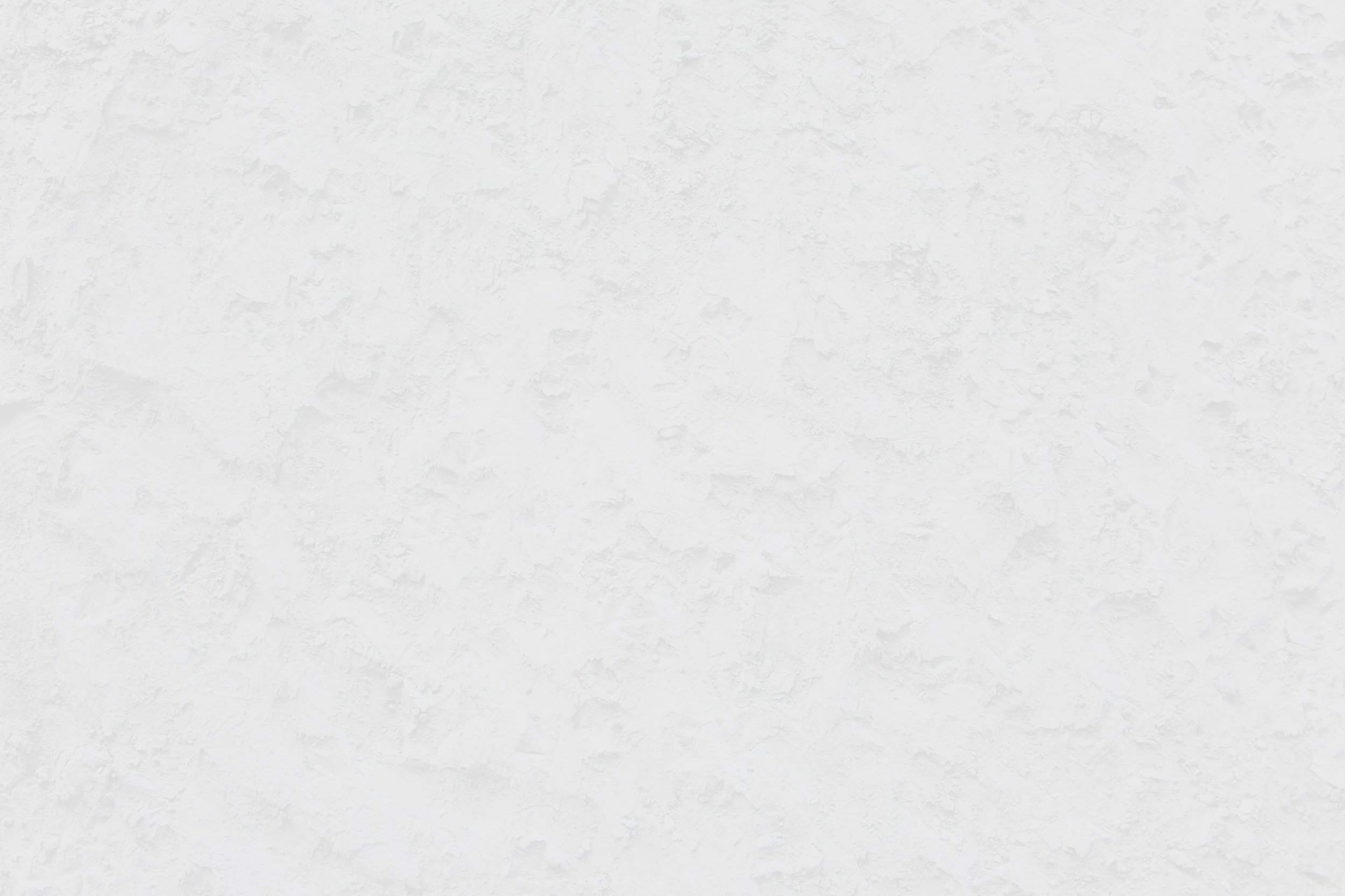
Implementing an Effective Fall Safety Program Can Have Serious Impacts
Author, Casey Craig, Account Executive, Rancho Mesa Insurance Services, Inc.
Year after year, falls are among the leading type of workers’ compensation claims and generate the highest claim costs. They account for multiple infractions on the top 10 most frequently cited standards, according to the Occupational Safety and Health Administration. How can you, as a business owner, control your exposure and keep your employees productive and healthy?
Author, Casey Craig, Account Executive, Rancho Mesa Insurance Services, Inc.
Year after year, falls are among the leading type of workers’ compensation claims and generate the highest claim costs. They account for multiple infractions on the top 10 most frequently cited standards, according to the Occupational Safety and Health Administration. How can you, as a business owner, control your exposure and keep your employees productive and healthy?
Prevention
According to the Centers for Disease Control, “27% of the 900,380 nonfatal work injuries resulting in days away from work in 2018 were related to slips, trips, and falls.” That’s a shockingly large number especially when 100% of falls are preventable if you take the time to plan, according to the National Safety Council (NSC). The NSC recommends:
Walking a job before employees get there to ensure proper set up is achievable with the equipment you are bringing for that job.
Pay attention to environmental conditions such as wind, rain, or excessive heat.
Check your equipment frequently to ensure nothing is worn down or damaged.
Make sure employees are wearing the proper foot wear and other Personal Protective Equipment (PPE) items required for the individual job needs.
Having employees working on ladders or scaffolding is essential for some jobs, and fortunately is a risk you can control. In addition to evaluating the work site, the equipment, the environmental factors, and PPE needed, you should also evaluate the health and fitness of all employees. Factors to consider should include the employee’s:
Experience
Fitness level
Age
Height Matters
A fatal fall can happen at almost any height. According to the NSC, only 16% of fatal falls in 2016 occurred as a result of a fall from over 30 feet; however, 53% of fatal falls that year resulted from below 20 feet. Given this data, best practices would dictate that construction companies should step back and reevaluate the safety procedures they have in place and determine if any changes need to be made, particularly for jobs that are considered the lower heights.
RM365 Advantage Safety Star™ Program
To get your employees properly trained, we recommend enrolling in our RM365 Advantage Safety Star™ program that includes Fall Prevention training. This program includes fundamental safety topics that allows your foreman or key management team to go through internet-based safety trainings and earn their Safety Star certification. This program has shown to improve safety while helping to reduce your workers’ compensation premiums. Register to start your RM365 Advantage Safety Star™ program, today.
Rancho Mesa understands the exposure our clients face on a daily basis and can help implement safety procedures to mitigate these risks. Underestimating a project’s risk or undertraining employees is an exposure you can address.
If you would like help in reviewing your safety protocols and procedures or if you have further questions, do not hesitate to reach out to me at (619) 438-6900 or email me at ccraig@ranchomesa.com.
CAL/OSHA Adopts Written COVID-19 Prevention Plan
Author, Emily Marasso, Media Communications Assistant, Rancho Mesa Insurances Services, Inc.
On November 19, 2020, California’s Occupational Safety and Health Administration (Cal/OSHA) Standards Board adopted temporary emergency standards to protect workers from COVID-19. These standards are expected to go into effect November 30, 2020, upon approval from the Office of Administrative Law.
Author, Emily Marasso, Media Communications Assistant, Rancho Mesa Insurances Services, Inc.
On November 19, 2020, California’s Occupational Safety and Health Administration (Cal/OSHA) Standards Board adopted temporary emergency standards to protect workers from COVID-19. These standards are expected to go into effect November 30, 2020, upon approval from the Office of Administrative Law.
Now, what does this mean for California employers? It means employers must have a written COVID-19 Prevention Plan. This written plan must include and address specific key points outlined by Cal/OSHA. These standards require employers to establish a system for communicating information about prevention, positive cases to employees, how cases will be identified and evaluated, a process for investigation and responding to cases, correction of hazards, training, physical distancing requirements, face covering, site-specific controls, reporting/recordkeeping and access, preventing the spread of the virus to other employees and a defined return-to-work criteria after a COVID-19 recovery.
Rancho Mesa Insurance has developed a COVID-19 Prevention Plan template for its clients to assist in the implementation and compliance of the new standards. Updated versions may become available as the standards are approved by the end of the month.
In addition, Rancho Mesa’s Risk Management Center offers additional tools employers can utilize to make sure they are in compliance with the new standards. Track daily COVID-19 symptoms in the Audit Track screen and deploy free online COVID-19 training for all employees from any mobile device. Our library of COVID-19 resources continues to grow and is available for our clients to access from the Risk Management Center and the RM365 HRAdvantage Portal™.
For information on how to access these resources, please reach out to your Client Services contact.
AB 685 Creates New Notice and Reporting Requirements
Author, Sam Brown, Vice President of the Human Services Group, Rancho Mesa Insurance Services Inc.
On September 17th, 2020 Governor Gavin Newsom signed into law Senate Bill 1159 (SB 1159) and Assembly Bill 685 (AB 685), both COVID-19 related bills. Both pieces of legislation will impact how employers respond to incidents of COVID-19 infections. This article will help business owners understand AB 685’s heightened occupational health and safety rules. Employers also need to understand how AB 685 grants California’s Occupational Safety and Health Administration (Cal/OSHA) greater enforcement powers.
Author, Sam Brown, Vice President of the Human Services Group, Rancho Mesa Insurance Services Inc.
On September 17th, 2020 Governor Gavin Newsom signed into law Senate Bill 1159 (SB 1159) and Assembly Bill 685 (AB 685), both COVID-19 related bills.
Both pieces of legislation will impact how employers respond to incidents of COVID-19 infections. This article will help business owners and officers understand AB 685’s heightened occupational health and safety rules. Employers also need to understand how AB 685 grants California’s Occupational Safety and Health Administration (Cal/OSHA) greater enforcement powers.
Posting Requirements
AB 685 requires California employers to provide the following four notices within one business day of being informed of a potential COVID-19 exposure:
Provide a written notice to all employees, and to the employers of subcontracted employees, who were at the same worksite within the infectious period, notifying the employee that they may have been exposed to COVID-19. It must be reasonable to assume the employees will receive the notice within one day, whether that is through email, text, or written notification.
If the employee population includes represented employees, then the employer must also send notice to the exclusive representative of the affected bargaining unit.
The employer must also provide notice of any COVID-19 related benefits or leave rights under federal, state, and local laws, or in accordance with employer policy. The employer must also notify employees of their protections against retaliation and discrimination.
The employer must notify all employers, the employers of subcontracted employees, and any exclusive representative, of the employer’s plan to complete a disinfection and safety plan in accordance with federal Centers for Disease Control guidelines.
Employers are required to maintain records of these notices for at least three years. Failure to comply with the notice requirements may result in a civil penalty.
If an employer learns of an “outbreak” as defined by the California Department of Public Health (“CDPH”), the employer must also notify the appropriate public health agency within 48 hours with the names, occupation, and worksite of any “qualifying individuals” related to the “outbreak.”
Two exceptions to the notice and reporting requirements:
Health facilities as defined in Section 1250 of the Health and Safety Code, are not required to report an “outbreak” within 48 hours.
The notice requirements do not apply to exposures by employees whose regular duties include COVID-19 testing and screening, or care to individuals who have or who are suspected to have COVID-19, unless the “qualifying individual” is also an employee at the same worksite.
Authorized Shutdown
Under AB 685, if Cal/OSHA determines that a workplace or operation within a workplace exposes employees to a risk of COVID-19 infection, creating an imminent hazard to employees, Cal/OSHA is authorized to prohibit entry to the workplace or the performance of operation in question.
If your organization would benefit from guidance on these new employer requirements, please contact Rancho Mesa Insurance at (619) 937-0175.
Sources:
https://leginfo.legislature.ca.gov/faces/billTextClient.xhtml?bill_id=201920200AB685
SB 1159 Is Now Workers’ Compensation Law
Author, Dave Garcia, President, Rancho Mesa Insurance Services, Inc.
As expected, California Governor Newsom signed Senate Bill 1159 (SB 1159) into law Thursday, September 17, 2020 and it will have several impacts on workers’ compensation and the presumption of the claim. Below is an outline of some of the more important elements of SB 1159. In simple terms, just remember three numbers, 4/4/14 - I’ll explain, later.
Author, Dave Garcia, President, Rancho Mesa Insurance Services, Inc.
As expected, California Governor Newsom signed Senate Bill 1159 (SB 1159) into law Thursday, September 17, 2020 and it will have several impacts on workers’ compensation and the presumption of the claim. Below is an outline of some of the more important elements of SB 1159. In simple terms, just remember three numbers, 4/4/14 - I’ll explain, later. Additionally, these rules will continue, unless modified, until January 2023. So, SB 1159 may be around for a while.
If an “outbreak” occurs, for the presumption of the claim to rest with the employer (meaning it will be presumed the person testing positive for COVID-19 contracted it at work and is therefore eligible for workers’ compensation benefits), there are several factors that need to be meet for that to occur.
If the employer has fewer than 100 employees and 4 employees test positive, or if the employer has more than 100 employees and 4% of their total employees test positive, during a 14-day period at an employer’s specific location, the COVID-19 case is presumed to be work-related. Thus, the 4/4/14 rule. When in doubt, call your workers’ compensation carrier and discuss the specific situation. They will help you determine whether or not it is a workers’ compensation claim.
Rob Darby, President of Berkshire Hathaway Homestate Companies, the second largest writer of workers’ compensation insurance in California and I discuss SB 1159 in a recent StudioOne™ Safety and Risk Management Network podcast episode “SB 1159 Impacts Workers' Comp Market.” A week before Governor Newsom signed the bill, Rob and I discussed the impacts of the bill to get an early insight. Take a listen - I think you will find it useful.
Now comes possible confusion with SB 1159. What is considered an outbreak? What is the definition of a specific location?
Outbreaks
The section of the law (Labor Code 3212.88) applies to any employee other than frontline workers and healthcare workers who test positive during an “outbreak” at the employer’s place of business, if the employer has 5 or more employees.
COVID-19 is presumed work-related if an employee worked at the employer’s place of business at the employer’s direction on or after July 6, 2020 and both the following elements are met:
The employee tested positive for COVID-19 within 14 days after working at the employer’s location.
The positive test occurred during an “outbreak” at the employer’s specific location.
An “outbreak” is defined as a COVID-19 occurrence at a specific employment location within a 14-day period AND meets one of the following:
If an employer has 100 employees or less at a specific location and 4 or more employees test positive for COVID-19;
If an employer has more than 100 employees at a specific location and 4% of the employees test positive for COVID-19;
The local public health department, State California Department of Public Health or Occupational Safety and Health Administration (Cal/OSHA) or school superintendent orders the specific place of employment to close due to risk of COVID-19 infection.
A specific location or place of employment is a building, store, facility or agricultural field where an employee performs work at the employer’s direction. An employee’s home is not considered a specific place of employment unless the employee provides home health care services to a client at the employee’s home. An employee may have more than one specific place of employment, if they worked in multiple locations within the 14-day period before their positive test.
There is a 45-day timeframe to determine if a positive COVID-19 case meets the above standard.
Outbreak Reporting Requirements
When an employer knows or reasonably should know that an employee has tested positive for COVID-19, they must report the incident to their workers’ compensation carrier. They should be prepared with the following information to give the carrier.
The fact that an employee has tested positive, regardless if work-related or not.
Employers should not include any personal information regarding the employee who tested positive for COVID-19 unless the employee asserts it is work-related or files a claim form.
The date the specimen was collected for the employee’s COVID-19 test.
The specific address or location of the employee’s place(s) of employment during the 14-day period preceding the date the test specimen was collected.
The highest number of employees who reported to work at the specific location(s) in the 45-day period before the last day the COVID-19 positive employee worked there.
It best practices to follow all local, state and federal guidelines for safe workplaces. However, even with the best intentions and precautions, COVID-19 may accidentally spread to employees. Again, when in doubt, report an employee COVID-19 case to your workers’ compensation carrier and allow them to determine how to proceed.
For questions about SB 1159 and how it with affect your organization’s workers’ compensation, contact your broker or reach out to Rancho Mesa at (619) 937-0164.
Court Agrees Temporary COVID-19 Standards Are Not Needed
Author, Emily Marasso, Media Communications Assistant, Rancho Mesa Insurance Services, Inc.
On June 11th, 2020, the D.C. Circuit Court denied the American Federation of Labor and Congress of Industrial Organizations’ (AFL-CIO) lawsuit against the Occupational Safety and Health Administration (OSHA) for not issuing an emergency temporary worker safety standard due to COVID-19.
Author, Emily Marasso, Media Communications Assistant, Rancho Mesa Insurance Services, Inc.
On June 11th, 2020, the D.C. Circuit Court denied the American Federation of Labor and Congress of Industrial Organizations’ (AFL-CIO) lawsuit against the Occupational Safety and Health Administration (OSHA) for not issuing an emergency temporary worker safety standard due to COVID-19.
As a volunteer labor union group that works to improve the lives of the U.S. workforce, the AFL-CIO wants OSHA to issue a temporary worker safety standard addressing the risks of COVID-19 in the workplace. However, an Emergency Temporary Standard is authorized by OSHA under certain limited conditions. It must be determined that workers are in danger of exposure to toxic substances or agents that can be physically harmful. Plus, a temporary standard then serves as a proposed permanent standard.
The D.C. Circuit Court denied the lawsuit against OSHA due to the fact that government officials are learning new information about COVID-19 weekly, if not daily. An appropriate response to the union’s concern is not a fixed rule, at this time. And, a standard specific to COVID-19 would likely not need to become a permanent standard in the future.
Furthermore, the U.S. Department of Labor states, "We are pleased with the decision from the D.C. Circuit, which agreed that OSHA reasonably determined that its existing statutory and regulatory tools are protecting America's workers and that an emergency temporary standard is not necessary at this time.”
While a new standard to combat COVID-19 isn’t necessary because of existing standards, OSHA has provided many resources for employers to assist in maintaining worker safety. Their “Guidance on Preparing Workplaces for COVID-19” provides information on the virus, how it could affect a workplace, steps employers can take to reduce the risk to employees, and additional services and programs available to employers. The “Guidance on Returning to Work” offers steps for reopening, applicable OSHA Standards, and a frequently asked questions section. In addition, employers can find news updates and resources on OSHA’s COVID-19 webpage.
OSHA Recording Requirements for COVID-19 Cases
Author, Alyssa Burley, Media Communications and Client Services Manager, Rancho Mesa Insurance Services, Inc.
As businesses begin to reopen across the country, employers are now faced with the real possibility that one or more of their employees may be diagnosed with COVID-19. Those who are familiar with the U.S. Department of Labor’s Occupational Safety and Health Administration (OSHA) recording requirements may be wondering how to handle an employee COVID-19 case on their OSHA logs.
Author, Alyssa Burley, Media Communications and Client Services Manager, Rancho Mesa Insurance Services, Inc.
As businesses begin to reopen across the country, employers are now faced with the real possibility that one or more of their employees may be diagnosed with COVID-19. Those who are familiar with the U.S. Department of Labor’s Occupational Safety and Health Administration (OSHA) recording requirements may be wondering how to handle an employee COVID-19 case on their OSHA logs.
California’s Division of Occupational Safety and Health (better known as Cal/OSHA) has released information for employers on the subject and it appears they are using their existing criteria for determining the recordability of an employee COVID-19 case.
According to Cal/OSHA, “California employers that are required to record work-related fatalities, injuries and illnesses must record a work-related COVID-19 fatality or illness like any other illness.” To be recordable on the 300, 300A and 301 forms, the COVID-19 case must be work-related and result in one of the following:
Death.
Days away from work or transfer to another job.
Medical treatment beyond first aid.
Loss of consciousness.
A significant injury or illness diagnosed by a physician or other licensed health care professional.
The criteria that most employers may have a hard time determining is if the COVID-19 illness is actually work-related. Cal/OSHA addresses this in its Frequently Asked Questions webpage. First, the employer must determine if there was “an event or exposure in the work environment [that] either caused or contributed to” the COVID-19 case.
In order to determine if a case is work-related, employers should consider factors like:
The type and duration of contact the employee had at work with other people including co-workers and the general public.
With the implementation of physical distancing and other controls within the workplace, what is the likelihood of exposure?
Did the employee come in contact with anyone showing signs and symptoms of COVID-19, while working?
These considerations will help an employer determine whether or not the COVID-19 case is work-related and thus recordable. According to Cal/OSHA, it is best practices to err on the side of recordability when in doubt about how an employee was exposed to COVID-19.
If it is determined that an employee’s illness was work-related, yet, for a variety of reasons testing or the results from a test is unavailable and the employee has been determined to have COVID-19, “an employer must make a recordability determination” as to whether or not to record the case. While a positive COVID-19 test result would trigger recordability by the employer, a positive test is not always necessary to record the case in the OSHA logs.
Keep in mind, the above information is for OSHA recording of work-related COVID-19 cases only, which may be different from guidance for workers’ compensation claims.
Cal/OSHA states that “Governor Newsom’s Executive Order N-62-20 addresses eligibility for workers’ compensation benefits... The Order does not alter employers’ reporting and recording obligations under Cal/OSHA regulations.”
Rancho Mesa’s Risk Management Center offers employers the ability to track their COVID-19 cases electronically and generate the applicable OSHA 300, 300A and 301 forms along with an incident report and First Report of Jury (Form 5020).
To learn more about the Risk Management Center, contact our Clients Services Department at (619) 438-6869.
Aerial Lift Best Practices
Author, Rory Anderson, Account Executive, Rancho Mesa Insurance Services, Inc.
Aerial lifts have become extremely popular over the past few years in the arboriculture industry. An aerial lift is an ideal way to reach higher trees safely and securely. They can also make potentially hazardous tree removal safer and more efficient. This equipment requires extensive training to operate responsibly, and the lack of this training has led to an increase in accidents and injuries with aerial lift devices.
Author, Rory Anderson, Account Executive, Rancho Mesa Insurance Services, Inc.
Aerial lifts have become extremely popular over the past few years in the arboriculture industry. An aerial lift is an ideal way to reach higher trees safely and securely. They can also make potentially hazardous tree removal safer and more efficient. This equipment requires extensive training to operate responsibly, and the lack of this training has led to an increase in accidents and injuries with aerial lift devices. According to OSHA, between 2009 and 2013 there were 47 aerial lift operator fatalities among the tree care industry in the US. To make for a safer operation, here are a few suggestions and reminders about Best Practices for working with aerial lifts:
Inspect the Lift
Visual inspections ensure that lifts remain functional and safe, while often saving potentially hours of maintenance and future medical bills. Conducting the visual inspection should include a close eye on hydraulic leaks, cracks, loose bolts, and worn or discolored hoses. It’s important to remember to always be cautious and not use your hands or any body parts to check for hydraulic-fluid leaks - always use a piece of cardboard or wood. When hydraulic fluid is under pressure, it can penetrate deep into skin and poison flesh, causing disastrous injuries. Never stick your hand around a fitting or hose to feel for a leak.
Function Testing and Drift Testing
Before climbing into the bucket, lift operators should check the lower controls and run the lift through a full range of motion. These controls are critical as they could very well come into use while rescuing a lift operator from the bucket in an emergency situation.
After the lower controls have been tested, a drift test should also be performed to make sure there are no issues with the hydraulics. To test for drift, set a traffic cone off to the side of the lift and move the bucket over the top of the cone, leaving a few inches in between. Turn the truck off and wait five minutes to make sure the boom doesn't drift down and touch the cone. If it does drift, take the truck out of service until it can be repaired.
Suiting Up
It is now time to put on your fall-protection harness. Make sure your harness fits properly and has a dorsal attachment. Once your harness is on, attach your fall restraint system to the harness and then to the life support attachment on the lift. It is virtually impossible to fall out of an aerial lift device if you wear proper fall protection and make sure it’s attached to the lift, every time.
When used correctly, aerial lifts can be effective and efficient tools for Arborists. When properly set up and tested, they can move easily on the jobsite and provide safe access in hard to reach areas. Their design allows for mobility and flexibility which can increase the crew’s safety, production and profitability.
Rancho Mesa’s Risk Management Center offers training materials covering aerial lifts, elevated work platforms and fall protection as online courses, tailgate talks and posters, as well as sample evaluation forms and policies. For additional information on the use of aerial lifts or other Best Practice safety measures for the arborist industry, please reach out to me, Rory Anderson at randerson@ranchomesa.com and learn more about our TreeOne Program.
What Employers Need to Know Before a Serious Injury Occurs in the Workplace
Author, Jim Malone, Workers’ Compensation Claims Advocate, Rancho Mesa Insurance Services, Inc.
Timely reporting of an employee’s work-related serious injury, illness or death can pose a challenge to the employer. As of January 1, 2020, these incidents (including any hospitalizations, unless the injured worker is admitted for medical observation or diagnostic testing) must be reported immediately to Cal/OSHA. Immediately means as soon as practically possible but not longer than 8 hours after the employer knows or, with diligent inquiry, would have known of the serious injury, illness or death.
Author, Jim Malone, Workers’ Compensation Claims Advocate, Rancho Mesa Insurance Services, Inc.
Timely reporting of an employee’s work-related serious injury, illness or death can pose a challenge to the employer. As of January 1, 2020, these incidents (including any hospitalizations, unless the injured worker is admitted for medical observation or diagnostic testing) must be reported immediately to Cal/OSHA. Immediately means as soon as practically possible but not longer than 8 hours after the employer knows or, with diligent inquiry, would have known of the serious injury, illness or death.
Monitoring the employee’s status at a hospital can be difficult if the employer has not put in place procedures and policies that will authorize a healthcare provider to disclose information that is covered by the Health Insurance Portability and Accountability Act (HIPAA). For example, the employer must follow-up with the hospital providing care to the injured employee to determine if the incident must be reported to Cal/OSHA. The employer will need to know if the employee has been moved from the emergency room and admitted to the hospital for in-patient treatment.
Ensuring policies and procedures are developed and implemented to restrict the use and disclosure of protected health information (PHI), are important elements of HIPAA compliance. If health information is used for purposes not permitted by the HIPAA Privacy Rule, or is deliberately disclosed to individuals not authorized to receive the information, there are possible penalties for the covered entity or individual responsible.
HIPAA permits PHI to be used for healthcare operations, treatment purposes, and in connection with payment for healthcare services. It can be argued that employers need this information to comply with State and Federal OSHA laws. Information may be disclosed to third parties for said purposes, provided an appropriate relationship exists between the disclosing covered entity (i.e., the hospital) and the recipient’s covered entity or business associate (i.e., the employee or employer). A covered entity can only share PHI with another covered entity if the recipient had previously or currently has a treatment relationship with the patient. The PHI has to relate to that relationship. In the case of a disclosure to a business associate, a Business Associate Agreement must have been obtained. Disclosures must be restricted to the minimum necessary information that will allow the recipient to accomplish the intended purpose of use.
Prior to any use or disclosure of health information that is not expressly permitted by the HIPAA Privacy Rule, one of two steps must be taken:
A HIPAA authorization must be obtained from a patient, in writing, permitting the covered entity or business associate to use the data for a specific purpose not otherwise permitted under HIPAA.
The health information must be stripped of all information that allows a patient to be identified.
Employers may consider obtaining signed business associate agreements or HIPAA authorizations from their employees before any injury or accident occurs. This will ensure they are able to get the appropriate protected medical information from the hospitals so they can report “serious injury or illness” accurately and timely to Cal/OSHA.
Therefore, it is extremely important for employers to learn the existing laws and new changes to these laws and have a plan of action in place to address these concerns before the next serious injury, illness, or death occurs.
Currently, reporting to Cal/OSHA can be made by telephone or e-mail. With these reporting changes, Cal/OSHA has also been directed to establish an on-line mechanism for reporting these injuries. It is always important to document when these incidents are reported to Cal/OSHA. Until an online mechanism is established, use of e-mail would be such method for documentation. Monitoring of the Cal/OSHA website for implementation of the on-line mechanism of reporting is also suggested.
For more information on how to report serious injuries and illnesses to Cal/OSHA, please reference “Cal/OSHA Updates: AB 1804 Changes How Injuries and Illnesses Are Reported.”
For more information about what is considered a serious injury or illness under Cal/OSHA, please reference “Cal/OSHA Updates: AB 1805 Changes Definition of Serious Injury or Illness.”
OSHA Penalties Increase in 2020
Author, Lauren Stumpf, Media Communications Coordinator, Rancho Mesa Insurance Services, Inc.
On January 15, 2020 the Federal Register published the Federal Civil Penalties Inflation Adjustment Act Annual Adjustments for 2020. This final rule increases civil penalties the Department of Labor assesses including those issued by the Occupational Safety and Health Administration (OSHA) based on workplace inspections and potential violations of safety and health standards. The rule is effective January 15, 2020. Beginning January 16, 2020 OSHA civil penalties will increase.
Author, Lauren Stumpf, Media Communications Coordinator, Rancho Mesa Insurance Services, Inc.
On January 15, 2020 the Federal Register published the Federal Civil Penalties Inflation Adjustment Act Annual Adjustments for 2020. This final rule increases civil penalties the Department of Labor assesses including those issued by the Occupational Safety and Health Administration (OSHA) based on workplace inspections and potential violations of safety and health standards. The rule is effective January 15, 2020. Beginning January 16, 2020 OSHA civil penalties will increase.
The new 2020 maximum OSHA penalties are as follows:
Serious violation: $13,494 (increased from $13,260)
Other-than-Serious violation: $13,494 (increased from $13,260)
Repeat violation: $134,937 (increased from $132,589)
Willful violation: $134,937 (increased from $132,589)
Each failure to correct the violation: $13,494 (increased from $13,260)
Each posting requirement violation: $13,494 (increased from $13,260)
For more information about the OSHA Penalties, visit https://www.osha.gov/penalties.
Cal/OSHA Updates: AB 1804 Changes How Injuries and Illnesses Are Reported
Author, Emily Marasso, Media Communications Assistant, Rancho Mesa Insurance Services, Inc.
As of January 1, 2020, California Assembly Bill 1804 (AB 1804) changed how an employer reports a serious employee injury or illness to Cal/OSHA. The bill removes the option to submit the report via email and replaces it with an “online mechanism,” according to Labor Code section 6409.1 (b). Reports may continue to be made via phone.
Author, Emily Marasso, Media Communications Assistant, Rancho Mesa Insurance Services, Inc.
As of January 1, 2020, California Assembly Bill 1804 (AB 1804) changed how an employer reports a serious employee injury or illness to Cal/OSHA. The bill removes the option to submit the report via email and replaces it with an “online mechanism,” according to Labor Code section 6409.1 (b). Reports may continue to be made via phone.
Until Cal/OSHA implements an online mechanism for collecting serious injury and illness reports like Fed/OSHA, emailed reports will be accepted. However, reports submitted by phone are always recommended over an emailed report. Reports submitted via phone or an online mechanism allows Cal/OSHA to ensure vital information is collected that is necessary to evaluate the seriousness of the injury or illness.
Cal/OSHA has not provided an estimated implementation date for the online report submission option.
As a reminder, California employers are required to report serious injury or illness of employees immediately. Serious injuries or illnesses must be reported as soon as practically possible. Deaths must be reported within 8 hours. All other injuries or illnesses must be reported once the employer learns of or should have known of the serious injury or illness.
2020 Promises Growth for Contractors but With a Twist
Author, Kevin Howard, C.R.I.S., Account Executive, Rancho Mesa Insurance Services, Inc.
Based on a recently published survey from the Associated General Contractors of America, 80% of contractors predict growth in 2020…but there is a twist. There is a major labor shortage.
Author, Kevin Howard, C.R.I.S., Account Executive, Rancho Mesa Insurance Services, Inc.
Based on a recently published survey from the Associated General Contractors of America, 80% of contractors predict growth in 2020…but there is a twist. There is a major labor shortage.
The current California Unemployment Rate, is a staggeringly low 3.9% compared to an unbearable 12% during the 2008 recession. As Californians, this statistic is music to our ears. However, for construction owners, the demand to hire skilled workers from an extremely shallow workforce pool has created a need for Best Practices hiring strategies paired with enhanced methods of retaining employees.
As a 13-consecutive year Best Practices Agency, Rancho Mesa provides resources to equip our clients with strategies and methods to enhance human resources strategies. These efforts lead to broader protection from insurable risk.
We are excited to partner with Equal Parts Consulting on February 6, 2020 for a seminar that will equip businesses with the needed methods for this economic environment. Attendees can look forward to the following topics and discussions below:
Strategies and best practices to create an easy to implement hiring process that aligns with your company’s culture.
Effective ways to assess and evaluate talent to ensure they are aligned with your company purpose, values, and culture.
Uncover some of the most important things your business can do to attract and retain the right talent for your culture.
Our goal is to help our contractor clients map out a game plan that will help retain talent, search for needed key employees and create a successful 2020 and beyond. Please feel free to contact me with any questions, at (619) 438-6874.
OSHA Offers Grant Programs to Nonprofits
Author, Sam Brown, Vice President, Human Services Group, Rancho Mesa Insurance Services, Inc.
Nonprofit leaders who want to make workplace safety training more accessible may be surprised to learn about a unique grant program through the Occupational Safety and Health Administration (OSHA). Since 1978, OSHA has offered grants to nonprofit organizations for safety training. Specifically, grants are awarded on a competitive basis to provide employees with training on the recognition and prevention of safety/health hazards in the workplace. The intent of the program is to reach audiences who might not otherwise receive safety training.
Author, Sam Brown, Vice President, Human Services Group, Rancho Mesa Insurance Services, Inc.
Nonprofit leaders who want to make workplace safety training more accessible may be surprised to learn about a unique grant program through the Occupational Safety and Health Administration (OSHA).
Since 1978, OSHA has offered grants to nonprofit organizations for safety training. Specifically, grants are awarded on a competitive basis to provide employees with training on the recognition and prevention of safety/health hazards in the workplace. The intent of the program is to reach audiences who might not otherwise receive safety training. OSHA renamed the program the Susan Harwood Training Grant Program, in 1997.
Grant applications in the past have typically fallen into three categories:
Capacity Building: OSHA awards these grants to help an organization grow or build its capacity to provide safety and health training to target audiences; small business employees, hard-to-reach or low-literacy workers, and workers in vulnerable and high-hazard industries.
Targeted Topic: These grants focus on occupational safety and health hazards associated with one of the OSHA selected training topics.
Training Materials Development: Grantees develop training materials on one of the OSHA selected training topics.
Although state or local government agencies are not eligible to apply, nonprofit organizations, including qualifying community and faith-based organizations, employer associations, and labor unions may submit applications.
The Harwood solicitation for grant applications can be found on the government-wide Grants.gov website.
RM365 Safety Star Program May Lower Risk of Receiving OSHA’s Most Frequently Cited Violation
Author, Kevin Howard, CRIS, Account Executive, Rancho Mesa Insurance Services, Inc.
Rancho Mesa Insurance Services’ RM365 Advantage Safety Star Program™ checks several boxes for contractors who are looking to improve their safety culture and lower risk. The program provides safety training designed to reduce an organization’s probability of work-related injuries; thus, minimizing the likelihood of an OSHA citation when used in conjunction with the Risk Management Center tools.
Author, Kevin Howard, CRIS, Account Executive, Rancho Mesa Insurance Services, Inc.
Rancho Mesa Insurance Services’ RM365 Advantage Safety Star Program™ checks several boxes for contractors who are looking to improve their safety culture and lower risk. The program provides safety training designed to reduce an organization’s probability of work-related injuries; thus, minimizing the likelihood of an OSHA citation when used in conjunction with the Risk Management Center tools.
Encouraging a safety culture through proper training makes sense for employers. Fed OSHA’s, maximum fine for a non-serious violation is $12,600. A willful repeat violation, however, can cost an employer anywhere from $70,000 - $126,000.
According to the United States Department of Labor, the top 10 most frequently cited standards are:
Fall protection, construction
Hazard communication standard, general industry
Scaffolding, general requirements, construction
Respiratory protection
Control of hazardous energy (lockout/tagout), general
Ladders, construction
Powered industrial trucks, general industry
Fall Protection–Training Requirements
Machinery and Machine Guarding, general requirements
Eye and Face Protection
Avoiding OSHA’s #1 Violation
With Fall Protection being at the top of OSHA’s citation list, and one of the most frequent causes of workplace fatalities in construction, it is of the upmost importance to focus on it when developing a safety program.
Rancho Mesa’s Risk Management Center offers a number of safety trainings that cover all 10 of the most frequently cited standards listed above. Fall Protection is one of five modules, within the RM365 Advantage Safety Star Program that could potentially help avoid a severe injury and OSHA fines.
When Century Painting’s Eddie Lopez was asked to give his thoughts on becoming RM365 Safety Star certified, his response was sincere.
“Obtaining my RM365 Safety Star Certificate was not only fulfilling and educational as a safety manager, but it also helped me navigate through safety criteria that OSHA is expecting us to follow regardless,” said Eddie Lopez, Safety Manager for Century Painting Corp.
RM365 Advantage Safety Star Program™ is a comprehensive tool for contractors that are hoping to package several advantages into one single task. To learn more about how to enroll, please visit the Safety Star Program™ page or contact Rancho Mesa Insurance Services at (619) 937-0164.
To learn more about the Fall Protection in Construction requirements, visit Cal OSHA’s Safety & Health Fact Sheet. You will notice links dedicated to each industry down the left side of the page. This information can further help companies avoid a potential OSHA fine, and more importantly, protect employees.
Top 5 Free Safety Apps for Landscape Contractors
Author, Drew Garcia, Vice President, Landscape Group, Rancho Mesa Insurance Services, Inc.
Mobile devices have become an invaluable tool for many people, on the job. They provide access to contacts, email and applications (i.e., apps) that can make work a lot simpler and safer for landscapers. We researched the top apps that boost worker safety. In no particular order, here are the top 5 free safety applications for the landscape industry.
Author, Drew Garcia, Vice President, Landscape Group, Rancho Mesa Insurance Services, Inc.
Mobile devices have become an invaluable tool for many people, on the job. They provide access to contacts, email and applications (i.e., apps) that can make work a lot simpler and safer for landscapers. We researched the top apps that boost worker safety. In no particular order, here are the top 5 free safety applications for the landscape industry.
OSHA-NIOSH Heat Safety Tool
This app allows workers and supervisors to monitor the heat index for any jobsite. By utilizing the apps features any user can get a reminder about the proper safety precautions and proactive measures that should be taken under the given conditions. It is available in both English and Spanish (to access Spanish, set phone language to Spanish).
Red Cross First Aid
This app provides access to information on how to properly handle first aid emergencies. It is available in both English and Spanish.
Chemical Safety Data Sheets - ICSC
This concise app offers searchable information on substances, delivered in a simple manner. It is only available in English.
NIOSH Sound Level Meter
This app quickly monitors the level of noise exposure in order to judge and evaluate if further testing is needed. It is available in both English and Spanish.
NIOSH Ladder Safety
This interactive ladder safety application is used to assist the worker in positioning a ladder at an optimal angle. It is available in both English and Spanish.
There are many applications employers can use on devices to help improve their safety program, formalize trainings, and consolidate information.
If you use an application (with or without a fee), we would like to hear about it, so we can share with all of our safety-minded clients. Please send your feedback to Alyssa Burley, aburley@ranchomesa.com.
Stay Off OSHA's Radar with an Effective Ladder Safety Program
Author, Casey Craig, Account Executive, Construction Group, Rancho Mesa Insurance Services, Inc.
Year after year OSHA publishes the “Top 10 Most Cited Violations” and it always seems to include violations dealing with falls. Fall protection, scaffolding, ladders, and fall protection (training requirements) all made this list and all of them have been on this list perennially for over a decade. How can a company that is using ladders keep from becoming just another name on the list of violators? How can you ensure that your employees are using provided equipment properly?
Author, Casey Craig, Account Executive, Construction Group, Rancho Mesa Insurance Services, Inc.
Year after year OSHA publishes the “Top 10 Most Cited Violations” and it always seems to include violations dealing with falls. Fall protection, scaffolding, ladders, and fall protection (training requirements) all made this list and all of them have been on this list perennially for over a decade. How can a company that is using ladders keep from becoming just another name on the list of violators? How can you ensure that your employees are using provided equipment properly?
The biggest mistake made with work at height is letting your employees perform their work using materials that are not meant for that job. Employees finding a chair, bucket, or truck to stand on to get those couple extra feet are the easiest ways to lead to an accident. From A-frames to extensions and step stools, there is a perfect tool for the job at hand. It does take a little preparation before sending your employees onto the job site. Having your supervisors make sure ladders are properly set up and fully functional to ensure your employees safety is as important as training your employees how to use a ladder.
Ladders have not miraculously become safer over the years. The materials used in making ladders may have changed, but the injuries that occur from using them have been the same. Here are some common misuses:
Trying to overextend reach at the top of a ladder, instead of taking the time to get all the way to the bottom to move the ladder and maintain three points of contact.
Stepping off from the third rung instead of keeping three points of contact all the way to the ground.
Setting the ladder at the wrong angle before climbing (70-75 degrees is desirable).
Trying to move a 70 pound ladder without asking for help and losing control.
There are countless ways that rushing or not paying attention to detail can leads to injuries. The American Ladder Institute (ALI) claims all injuries that occur on a ladder are preventable with the proper attention to detail. If you know that a ladder has a bent rung, or the frame is compromised, the risk is not worth having an employee get on that ladder. Ladders are manufactured to withhold four times the weight they are rated for, but if damaged there is no telling what could make it catastrophically defective. Make sure that there is enough tread on the foot of the ladder to keep your ladder in place while working at height.
Now that we know a little about our exposure, let’s see what we can do to fix the problem. Making sure you have the right equipment is by far the most important step to keep you from running into a violation. Keep your employees trained in proper ladder safety, and only let the employees that have been trained on a ladder. Properly tie off ladders, maintain your equipment over time, and attend ladder safety seminars regularly. One huge tool that is underutilized in the construction industry is having a consultation meeting with OSHA. Have them come out and inform you of things you could be doing better without the worry of being fined. OSHA is meant to be a tool to keep your employees safe, don’t hesitate to use them.
For questions about ladder safety seminars or what policies may match your company’s risk, please contact Rancho Mesa Insurance Services, Inc. at (619) 937-0164. We look forward to helping better your risk profile.
Reporting Serious Workers’ Compensation Injuries
Author, Jim Malone, Workers’ CompensationClaims Advocate, Rancho Mesa Insurance Services, Inc.
Workers’ Compensation injuries occur every day. The majority of these injuries are minor incidents which require no medical treatment or loss of time from work. For others, the injury is reported to the insurance carrier, the injury is addressed, forms are provided, and the recovery from the injury is monitored until the employee is released back to work and a discharge from care is provided.
Author, Jim Malone, Workers’ CompensationClaims Advocate, Rancho Mesa Insurance Services, Inc.
Workers’ Compensation injuries occur every day. The majority of these injuries are minor incidents which require no medical treatment or loss of time from work. For others, the injury is reported to the insurance carrier, the injury is addressed, forms are provided, and the recovery from the injury is monitored until the employee is released back to work and a discharge from care is provided.
However, serious injuries, illnesses or even deaths occasionally occur at work because of a work related accident. These incidents usually require 911 calls, hospitalizations, emergency surgeries, family contact, and a longer road to recovery. They may also require immediate (within 8-24 hours) reporting to the California Occupational Safety and Health Administration (Cal/OSHA), if they meet the criterion that has been established.
As defined in the California Code of Regulations Title 8 §330(h), serious injury or illness means any injury or illness occurring in a place of employment, or in connection with any employment that:
Requires inpatient hospitalization for a period in excess of 24 hours for other than medical observation.
Results in a loss of any member of the body.
Results in a serious degree of permanent disfigurement.
Results in the death of the employee.
Does not include any injury, illness, or death caused by the commission of a Penal Code violation, except the violation of Section 385 of the Penal Code, or an accident on a public street or highway.
The California Code of Regulations Title 8 §342(a) states, “every employer shall report immediately by telephone or telegraph to the nearest District Office of the Division of Occupational Safety & Health any serious injury or illness, or death, of an employee occurring in a place of employment or in connection with any employment. Immediate means as soon as practically possible but not longer than 8 hours after the employer knows or with diligent inquiry would have known of the serious injury or illness. If the employer can demonstrate that exigent circumstances exist, the time frame for the report may be made no longer than 24 hours after the incident.”
The 8-24 hour time frame begins when the employer knows, or “with diligent inquiry” would have known of the serious injury, illness, or death. The “employer” means someone in a management or supervisory capacity.
As with any injury or accident, it can be a difficult and confusing time for all those involved and affected. It may seem like many things need to be done all at once. That is, of course, impossible. So, prepare yourself now. Make a list of your responsibilities and important contact numbers before a serious injury or accident occurs.
The order in which you perform each of these responsibilities may differ, according to the type of injury or accident that occurs. However, you will still have your checklist and contact numbers ready to use to ensure you do not forget any particular step or obligation. This emergency list of telephone numbers may be your broker, safety/loss control specialist, claims administrator, or workers’ compensation claims advocate. We are all available to provide you with any assistance you may need.
For those in California, the Cal/OSHA District Office contact list is below. Ask for the officer of the day.
Concord (925) 602-6517
Oakland (510) 622-2916
San Francisco (415) 972-8670
Cal/OSHA Link: www.dir.ca.gov/title8/342.html
For additional information, please contact Rancho Mesa Insurance Services, Inc. at (619) 937-0164.
The Hidden Gems in the OSHA Silica Regulation
Author, Glenn Ingraham, MS CIH.
If you’re complying with the OSHA Silica Standard for Construction by following the requirements in Table 1, then congratulations! You’re doing well. But do you know about the two little hidden gems in the standard? Those two requirements are connected to the use of respirators in Table 1.
Author, Glenn Ingraham, MS CIH, Technical Specialist, ICW Group Insurance Companies.
If you’re complying with the OSHA Silica Standard for Construction by following the requirements in Table 1, then congratulations! You’re doing well. But do you know about the two little hidden gems in the standard? Those two requirements are connected to the use of respirators in Table 1.
https://www.cdc.gov/niosh/npptl/pdfs/n95-infographic-mask-labeling.pdf
For those tasks that require a respirator, OSHA only says “APF 10”. You probably know that APF 10 means that the worker is to use either a filtering face-piece (dust mask), or a re-usable cartridge-equipped half-mask respirator. But do you know that being required to use a respirator during that task also means that your organization must write and implement a Respiratory Protection Program (RPP)? And that means all the bells and whistles such as respirator selection, medical clearance (OSHA Questionnaire), fit testing (initial and annual), and training.
The second little gem is a bit more technical. Because the Silica standard is focused on protecting workers from ‘Respirable Dust’ (very fine particles), then the respirator used must be capable of protecting against those extremely small dust particles. That’s no problem if your workers are using a re-usable ½ mask respirator with filter cartridges since those filter cartridges are HEPA filters, which protect against 99.97% of particles down to 0.3 microns. Very effective. But if you choose to use a dust mask, then you have to be careful. The most commonly used dust mask is the N-95. The ‘95’ means that the mask is only 95% effective against those small particles. So, you need a better dust mask. One that is equivalent to the HEPA filter. No problem. Just ask your supplier to provide you with a N-100 dust mask and you’re good to go!
And with regard to that letter ‘N’ in N-95: Sometimes dust masks are used to protect workers from exposure to oil mist. Dust masks that offer protection against oil mists have a ‘R’ (Oil Resistant) or a ‘P’ (Oil Proof) designation. Masks designated with ‘N’ are the least expensive (and most common) since they are NOT treated to provide protection against oil mists.
N-100 dust masks are made by Moldex, 3M, and other manufacturers. But wherever you buy your dust masks, be sure that they are always NIOSH approved. Beware cheap un-approved knock-offs!
Published with permission.
Source
Berkshire Hathaway's Steve Hamilton Discusses Workplace Injury Trends for the Landscape Industry in Recent Webinar
Author, Drew Garcia, NALP Program Director, Rancho Mesa Insurance Services, Inc.
In this webinar, Steve Hamilton, Senior Loss Control Specialist from Berkshire Hathaway Homestate Companies, reviews workplace injury trends for the landscape industry, along with OSHA’s most cited regulatory violations.
Author, Drew Garcia, NALP Program Director, Rancho Mesa Insurance Services, Inc.
Steve Hamilton, Senior Loss Control Specialist from Berkshire Hathaway Homestate Companies, reviews workplace injury trends for the landscape industry, along with OSHA’s most cited regulatory violations, in his Landscape Industry Injury Trends for 2017 webinar.
This information will help landscapers focus their training efforts to improve compliance and reduce the risk potential for frequency and severity.
Start the year off right with a plan to address these common injury trends!
A National Association of Landscape Professionals (NALP) login is required to view the webinar.
OSHA Begins Enforcement of New Silica Rule
Author, Alyssa Burley, Client Services Coordinator, Rancho Mesa Insurance Services, Inc.
After an initial delay and a 30-day grace period, the Occupational Safety and Health Administration‘s (OSHA) revised Crystalline Silica Rule is now in full effect. The rule became effective September 23, 2017 and OSHA allowed for a 30-day grace period for issuing fines and citations for companies who were making a good-faith effort towards meeting the new requirements.
Author, Alyssa Burley, Client Services Coordinator, Rancho Mesa Insurance Services, Inc.
After an initial delay and a 30-day grace period, the Occupational Safety and Health Administration‘s (OSHA) revised Crystalline Silica Rule is now in full effect. The rule became effective September 23, 2017 and OSHA allowed for a 30-day grace period for issuing fines and citations for companies who were making a good-faith effort towards meeting the new requirements.
“The new silica rule lowers the permissible exposure limit from the current standard of 250 micrograms per cubic meter of air to 50 micrograms per cubic meter of air, averaged over an eight hour day, and an action level of 25 micrograms per cubic meter of air,” wrote Sam Clayton, Vice President of Rancho Mesa Insurance Services’ Construction Group.
OSHA has made available Interim Enforcement Guidelines and a Fact Sheet to assist companies in complying with the new requirements.
To learn more about the Crystalline Silica rule, read “Is your company prepared for OSHA’s new Silica Rule?” by Sam Clayton.
Contact Rancho Mesa Insurance Services at (619) 937-0164 for more information.
OSHA Announces Top 10 Cited Violations for FY 2017
Author, Sam Clayton, Vice President, Construction Group, Rancho Mesa Insurance Services, Inc.
The Occupational Safety and Health Administration (OSHA) released its preliminary top 10 citation list for fiscal year 2017 at the annual National Safety Council (NSC) Congress and Expo, held in late September 2017.
Author, Sam Clayton, Vice President, Construction Group, Rancho Mesa Insurance Services, Inc.
The Occupational Safety and Health Administration (OSHA) released its preliminary top 10 citation list for fiscal year 2017 at the annual National Safety Council (NSC) Congress and Expo, held in late September 2017.
“One thing I’ve said before in the past on this is, this list doesn’t change too much from year to year,” said Patrick Kapust, deputy director of OSHA’s Directorate of Enforcement and Programs, during the expo presentation. “These things are readily fixable. I encourage folks to use this list and look at your own workplace.”
OSHA compiled the list using data collected from incidents occurring from October 2016 through September 2017.
- Fall Protection in Construction: 6,072 violations.
Frequently violated requirements include unprotected edges and open sides in residential construction and failure to provide fall protection on low-slope roofs - Hazard Communication: 4,176 violations.
Not having a hazard communication program topped the violations, followed by not having or providing access to safety data sheets - Scaffolding: 3,288 violations.
Frequent violations include improper access to surfaces and lack of guardrails - Respiratory Protection: 3,097 violations.
Failure to establish a respiratory protections program topped these violations, followed by failure to provide medical evaluations - Lockout/Tagout: 2,877 violations.
Frequent violations were inadequate worker training and inspections not completed. - Ladders in Construction: 2,241 violations.
Frequent violations include improper use of ladders, damaged ladders and using the top step. - Powered Industrial Trucks: 2,162 violations.
Violations include inadequate worker training and refresher training. - Machine Guarding: 1,933 violations.
Exposure points of operation topped these violations. - Fall Protection-training requirements: 1,523 violations.
Common violations include failure to train workers in identifying fall hazards and proper use of fall protection equipment. - Electrical-wiring methods: 1,405 violations.
Violations of this standard were found in most general industry sectors, including food and beverage, retail and manufacturing
Training materials for each of the items on the OSHA list are available within the Risk Management Center. Contact Rancho Mesa Insurance Services, Inc. at (619) 937-0164, for more information.