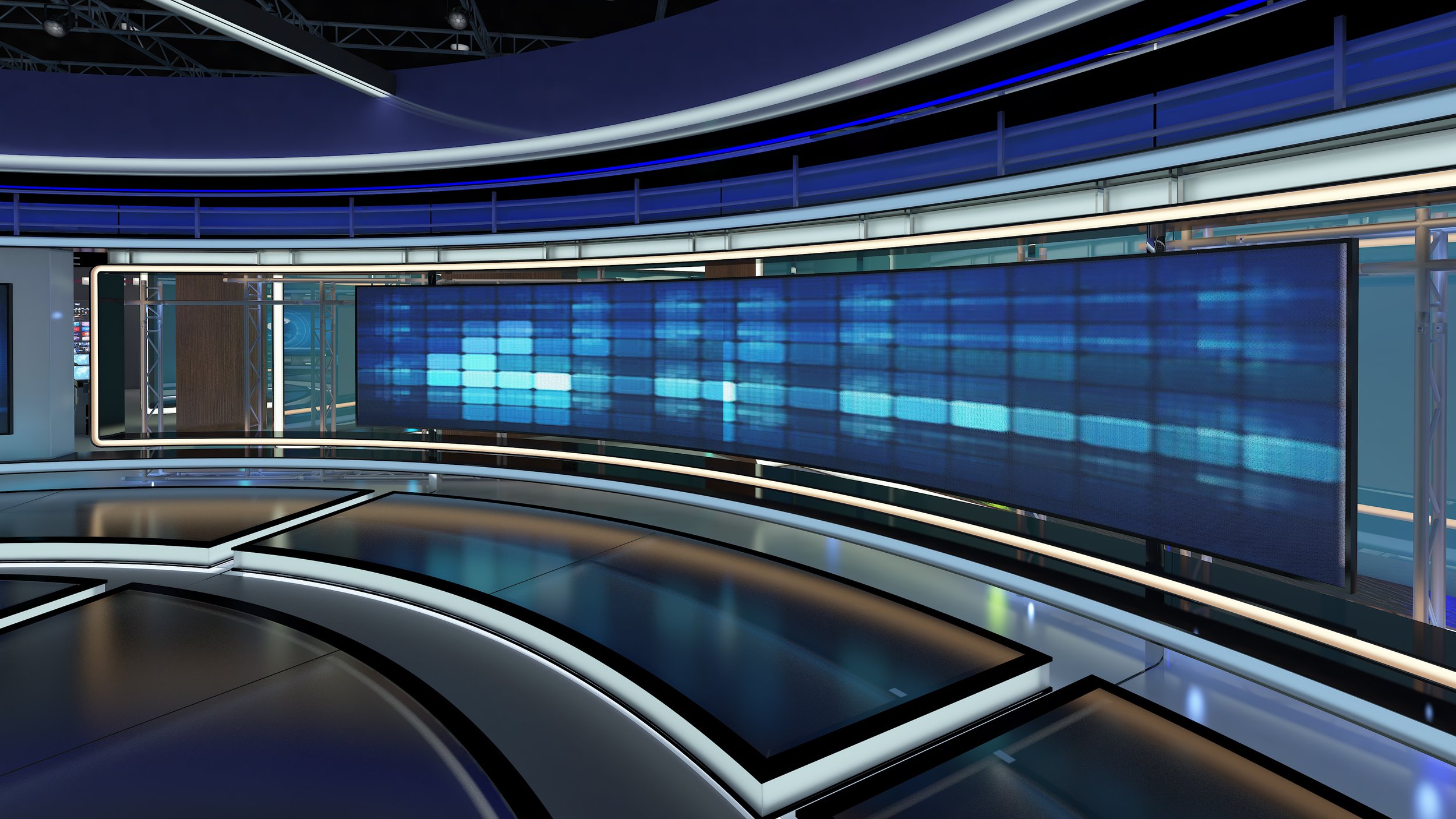
Industry News
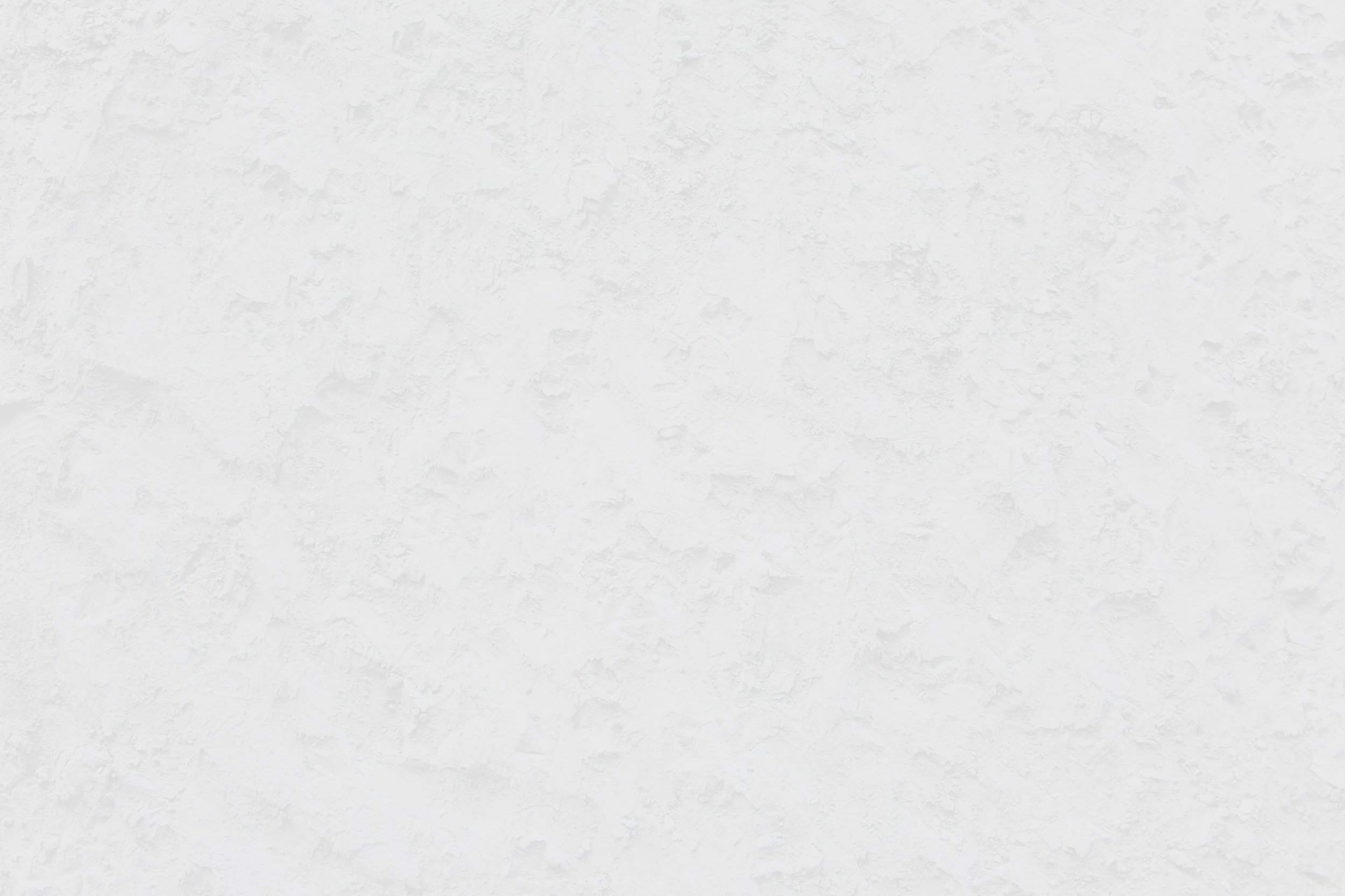
Is your Company Prepared for OSHA’s new Silica Rule?
Author, Sam Clayton, Vice President, Construction Group, Rancho Mesa Insurance Services, Inc.
On September 23rd 2017 the Occupational Safety and Health Administration’s (OSHA) new silica standard for construction will go into effect. This means contractors who engage in activities that create silica dust or are known in the industry as respirable crystalline silica, must meet a stricter standard for how much dust there workers inhale.
Author, Sam Clayton, Vice President, Construction Group, Rancho Mesa Insurance Services, Inc.
On September 23rd 2017 the Occupational Safety and Health Administration’s (OSHA) new silica standard for construction will go into effect. This means contractors who engage in activities that create silica dust or are known in the industry as respirable crystalline silica, must meet a stricter standard for how much dust their workers inhale.
What is Crystalline Silica?
Crystalline silica is a common mineral that is found in material that we see every day in roads, buildings and sidewalks. It is a common component of sand, stone, rock, concrete, brick, block and mortar.
What are the Effects?
Exposures to crystalline silica dust occur in common workplace operations involving cutting, sawing, drilling, and crushing of rock, and stone products such as construction tasks and operations using sand products like in glass manufacturing, foundries, sand blasting and hydraulic fracking. Inhaling silica dust can lead to silicosis, an incurable lung disease that can be fatal. Those with too much silica exposure can also develop lung cancer, kidney disease and chronic obstructive pulmonary disease.
What is the New Standard?
The new silica rule lowers the permissible exposure limit from the current standard of 250 micrograms per cubic meter of air to 50 micrograms per cubic meter of air, averaged over an eight hour day, and an action level of 25 micrograms per cubic meter of air.
How will the New Standard protect workers?
The rule significantly reduces the amount of silica dust that workers can be exposed to on the job. That means employers will have to implement controls and work practices that reduce workers exposures to silica dust. For most activities, that means employers will have to ensure the silica dust is wet or vacuumed up before workers can work in the area. Employers are required under the rule to provide training, respiratory protection when controls are not enough to limit exposure and written exposure control plans, measure controls in some cases limit access to high exposure areas. Employers are also required to offer medical exams to highly exposed workers.
How can your company protect itself from Silica Related Claims?
In addition to implementing the necessary controls to protect your employees, we would highly recommend you review your insurance policies to make sure that your company is protected from silica related claims.
Over the last few years, we’ve seen quite a few General Liability carriers putting Silica exclusions on there policies. This isn’t always the case and may be negotiated out depending on the carrier. Another alternative is to obtain a Contractors Pollution Policy that would provide the necessary coverage for this exposure.
Rancho Mesa also recommends taking advantage of the Silica Exposure Training materials available within the Risk Management Center. These materials include an online training course, PowerPoint presentation, training short and quiz in both English and Spanish. Should you have any questions, please contact Rancho Mesa Insurance Services at 619-937-0164.
OSHA Launches Inaugural Safe + Sound Week
Author, Alyssa Burley, Client Services Coordinator, Rancho Mesa Insurance Services, Inc.
The Occupational Safety and Health Administration (OSHA) launched its inaugural Safe + Sound Week, which runs from June 12 - 18, 2017. According to OSHA, Safe + Sound week is "a nationwide event to raise awareness and understanding of the value of safety and health programs that include management leadership, worker participation, and a systematic approach to finding and fixing hazards in workplaces."
Author, Alyssa Burley, Client Services Coordinator, Rancho Mesa Insurance Services, Inc.
The Occupational Safety and Health Administration (OSHA) launched its inaugural Safe + Sound Week, which runs from June 12 - 18, 2017. According to OSHA, Safe + Sound week is "a nationwide event to raise awareness and understanding of the value of safety and health programs that include management leadership, worker participation, and a systematic approach to finding and fixing hazards in workplaces."
Why should your company participate?
Workplace safety and health programs can help companies proactively identify and manage workplace hazards before they cause injury or illness. That is good news for companies and employees.
How can businesses participate?
There are three easy steps to participating in Safe + Sound Week. Visit OSHA's Safe + Sound Week webpage for more information on each of these steps:
Step 1: Select the activities you would like to do at your workplace. There are three activities to choose from: Management Leadership, Worker Participation, and Find and Fix Hazards.
Step 2: Plan and promote your events. OSHA has provided Event Tools, Graphics & Signage, Customizable Communications materials, Social Media (#SafeAndSound), and Recruitment Tools.
Step 3: Get recognized for your participation. Complete the online form to generate a Safe + Sound Week Certificate of Recognition and web badge for your organization.
OSHA Not Prepared to Accept Electronic Submissions
Author, Alyssa Burley, Client Services Coordinator, Rancho Mesa Insurance Services, Inc.
For over a year, the Occupational Safety and Health Administration (OSHA) have championed the upcoming electronic submission of injury and illness records (i.e., OSHA 300 logs) through its website. The new requirement was designed to make OSHA records publicly available on the internet in hopes that it would encourage employers to maintain safer working environments. The electronic submissions of the 2016 reports were supposed to be due by July 1, 2017.
Author, Alyssa Burley, Client Services Coordinator, Rancho Mesa Insurance Services, Inc.
For over a year, the Occupational Safety and Health Administration (OSHA) have championed the upcoming electronic submission of injury and illness records (i.e., OSHA 300 logs) through its website. The new requirement was designed to make OSHA records publicly available on the internet in hopes that it would encourage employers to maintain safer working environments. The electronic submissions of the 2016 reports were supposed to be due by July 1, 2017.
However, in a mid-May announcement, the government agency’s website declares “OSHA is not accepting electronic submissions of injury and illness logs at this time, and intends to propose extending the July 1, 2017 date by which certain employers are required to submit the information from their completed 2016 Form 300A electronically.”
According to an article on Front Page News, “several business groups, including the Associated Builders & Contractors, Association of General Contractors, and National Association of Home Builders, had challenged the 2016 Occupational Safety and Health Administration regulation in court and lobbied the administration to jettison it on grounds that it could unfairly damage the reputation of some of their members.”
In preparation of the anticipated electronic submission requirement, developers of Rancho Mesa’s Risk Management Center, an online platform designed for risk management, workplace safety and compliance have been ready and waiting for the details of OSHA’s API (application programing interface) in order to build a seamless integration between the two websites. Rancho Mesa will keep its clients up to date on the development of this integration, if and when it becomes operational on the OSHA website.
As for now, Rancho Mesa is urging its clients to continue to track incidents in the Risk Management Center so they may take advantage of its trending tools and reports.
For details regarding who must keep and report OSHA records, visit www.osha.gov/injuryreporting.
Sources:
“Injury Tracking Application: Electronic Submission of Injury and Illness Records to OSHA.” United States Department of Labor. Retrieved from: https://www.osha.gov/injuryreporting/.
“OSHA suspends rule requiring firms report injury, illness data electronically.” Front Page News. Retrieved from: http://www.advisen.com/tools/fpnproc/news_detail3.php?list_id=26&email=kvasquez@ranchomesa.com&tpl=news_detail3.tpl&dp=P&ad_scale=1&rid=283636777&adp=P&hkg=5cY58Bd37J