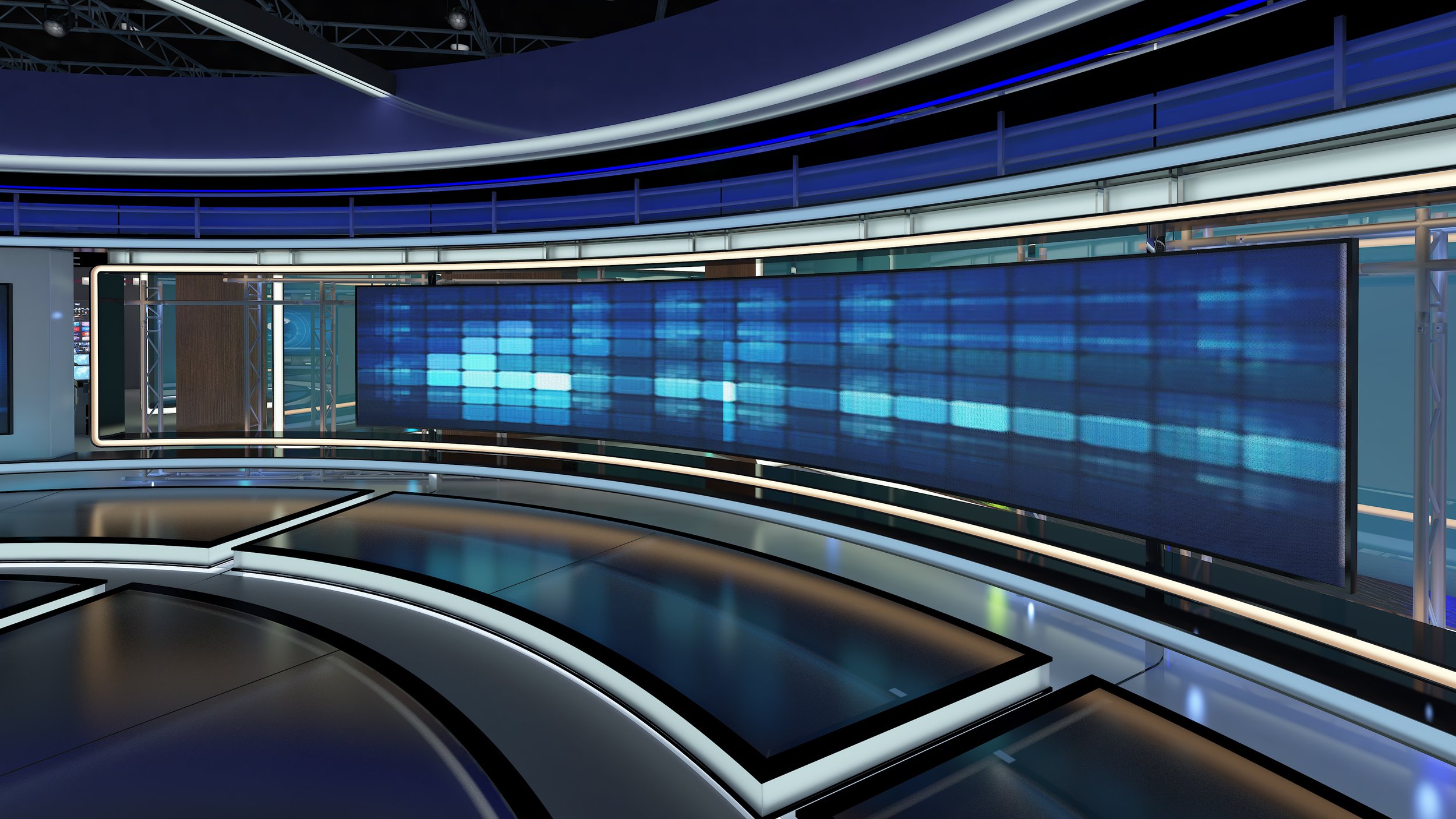
Industry News
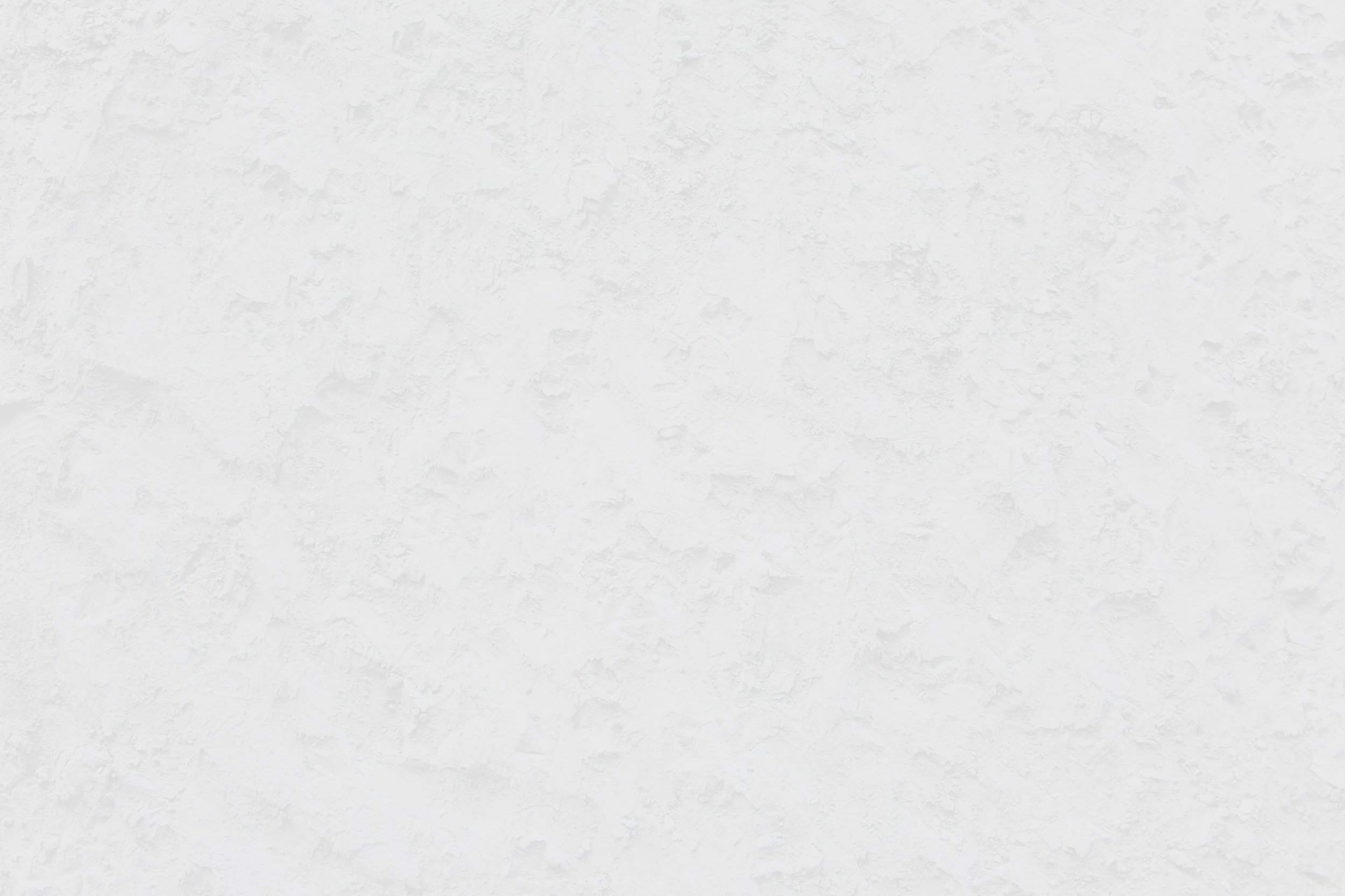
Three Changes to Your Routine That Increases Safety
Author, Greg Garcia, Account Executive, Landscape Group, Rancho Mesa Insurance Services, Inc.
Every landscape company wants to be safe. So, I want to discuss three ways to improve safety in your workplace starting today: routine equipment maintenance, personal protective equipment (PPE) checks, and finally, assessing job site hazards.
Author, Greg Garcia, Account Executive, Landscape Group, Rancho Mesa Insurance Services, Inc.
Every landscape company wants to be safe. So, I want to discuss three ways to improve safety in your workplace, starting today.
1) Routine Equipment Maintenance
Routine maintenance and cleaning of equipment is essential for any landscape company wanting to make sure all of their equipment is running properly and is ready for a day’s work. From a safety standpoint, we see the biggest risk comes from those companies who use sprayers to fertilize lawns and plants for their clients. By not cleaning the sprayers out daily, landscape companies are putting their employees at risk of being exposed to pesticides and herbicides, which can be detrimental to the employee’s heath. Therefore, routinely checking and cleaning pieces of equipment can not only improve your productivity and profitability by making sure equipment is ready for work, but can also lead to a much safer working environment for your employees.
2) personal protective equipment (PPE) checks
Personal protective equipment is one of the most important things landscape employees can use to protect themselves while they work. Whether it be thorny bushes to cut back, the use of loud chainsaws or mowers, or just the effects of being out in the sun, it is important to assess the job site hazards and make proper PPE choices. A few examples that landscape companies are doing to help their employees fight the effects of being exposed to the sun are: wearing long sleeve shirts, wearing sun hats that provide shade to the face and neck, and wearing proper sunglasses to help with the heavy glare. Always keeping up to date and staying informed on proper PPE will ensure that your landscape company is doing all they can to stay safe.
3) assessing job site hazards
Finally, addressing job site hazards is vital for companies in the landscape industry. The safety manager, supervisor or foreman need to get out to job sites and really see what hazards are out there. For example, look to see if there are any poisonous plants at the jobsite and/or any pieces of debris or puddles in the walk ways that could create a trip and fall hazard. All of these exposures need to be noted to ensure everyone is aware of potential risks. Every jobsite is different, so it is crucial that your team remain proactive and really hone in on the potential risks at each particular jobsite.
If equipment checks, PPE checks, and job site checks are not currently in your landscape company’s safety routine, I would strongly suggest starting that routine, today.
Subscribe to our weekly landscape-specific safety emails to ensure you are getting relevant training materials every week.
If you have questions about how to mitigate your company’s risk, reach out to Greg Garcia at (619) 438-6905 or ggarcia@ranchomesa.com.
Wearable Technology Is the Future of Jobsite Safety
Author, Sam Clayton, Vice President, Construction Group, Rancho Mesa Insurance Services, Inc.
The future is here and construction companies are starting to adopt wearable technology for their workers to reduce and prevent injuries from occurring on their jobsites. Wearable technology can be defined as any device that construction workers wear on his/her body. Since the construction industry accounts for nearly half of all fatal work injuries, this new type of personal protective equipment (PPE) is going to look radically different in the years ahead and should reduce both fatal and non-fatal injuries on jobsites worldwide. Below is an overview of five technologies in use today or soon to be in use in the near future.
Author, Sam Clayton, Vice President, Construction Group, Rancho Mesa Insurance Services, Inc.
The future is here and construction companies are starting to adopt wearable technology for their workers to reduce and prevent injuries from occurring on their jobsites. Wearable technology can be defined as any device that construction workers wear on his/her body. Since the construction industry accounts for nearly half of all fatal work injuries, this new type of personal protective equipment (PPE) is going to look radically different in the years ahead and should reduce both fatal and non-fatal injuries on jobsites worldwide. Below is an overview of five technologies in use today or soon to be in use in the near future.
Smart Watches
Many people wear smart watches daily, but the powerful sensors in smart watches can provide significant benefit to the construction industry. These devises can monitor vital signs like heart rate and step counts to prevent overexertion. They can also detect falls, which is a leading cause of serious injury on a jobsite and provide an immediate alert to site and emergency personal. In addition, smart watches allow employees hands free communication.
Smart Hard Hats
Hard hats are a vital piece of PPE on every jobsite. But, these aren’t your fathers’ hard hat. By adding a sensor band around the inside of a hard hat, employers will be able to detect fatigue, prevent mircosleeps (when sudden moments of sleep occur in a fatigued individual) and proximity sensing. Proximity sensing will alert both workers and equipment operators of a potential collision and prevent serious injuries. In addition, the outside rim of the smart hard hat is equipped with a ring of LED lights that allow for visibility from a quarter mile away. This feature is especially useful for any contractors performing work at night.
Clip-Ons
Clip-ons are not part of the usual construction PPE but are proving to be very helpful. A clip-on can identify zone-based worker locations and detect free falls. With a direct line of communication, workers can immediately report injures by pushing a button.
Smart Boots
Steel toe boots are already an essential for construction workers, but in the next few years the soles in these boots will be capable of detecting shocks and falls sustained by workers, track the location of the workers more accurately and will recharge themselves by walking in them.
Smart Vests
Highly visible vests are a staple on jobsites. These new vests can track body temperature and will alert workers when a break in the shade or a drink of water is necessary to prevent heat-related illnesses. The built-in sensors can also alert workers when they are nearing or entering a hazardous area. If used in conjunction with GPS equipped equipment, they can detect nearby equipment and slow them down to avoid any safety issues.
The future of construction safety will include some form of smart device that alerts the wearer and/or the safety manager when it detects a hazard. While these wearables are not a replacement for traditional PPE and best practices, they can help prevent hazards created by human error. As they are deployed across jobsites, we’ll be able to prevent workplace injuries before they happen.
For questions about managing your jobsite risk, contact me at sclayton@ranchomesa.com or (619) 937-0167.
Signing Up for Safety
Author, Greg Garcia, Account Executive, Landscape Group, Rancho Mesa Insurance Services, Inc.
There are many tips, ideas, and systems involved in creating a safe culture in the landscape industry. The most common practice landscape companies implement with regards to safety are regular safety meetings.
Author, Greg Garcia, Account Executive, Landscape Group, Rancho Mesa Insurance Services, Inc.
There are many tips, ideas, and systems involved in creating a safe culture in the landscape industry. The most common practice landscape companies implement with regards to safety are regular safety meetings.
For these meetings to be effective, you need to ask yourself three questions:
What should be discussed during these safety meetings?
How often do we really need to have these meetings?
Where can I find content for these meetings?
Let’s take a look at each question in more detail.
What should be discussed in these safety meetings? The easy answer is we will just talk about an accident that has recently occurred. That seems like a good approach, but it’s more of a reactive approach than proactive. Make no mistake about it, it is very important to go over safety regarding a previous incident, and take the necessary steps to help prevent that incident from happening again. However, a great safety culture includes a more proactive approach by covering safety topics before an incident occurs. Examples of good topics for safety meetings include something as simple as “Operating a Leaf Blower” to more pressing issues like “Handling Medical Emergencies and Jobsite Injuries.”
Secondly, how often do we need to hold these meetings? The quick answer as often as possible, but we recommend weekly safety meetings as they are the best way to create and change culture for the better. Weekly meetings build consistency. And, these good habits create a safety first culture by emphasizing safety and showing your employees that their wellbeing is a top priority. Plus, OSHA requires safety meetings at least every ten working days, so scheduling them weekly ensures you are meeting that requirement.
Finally, and what seems to be the most important question, is where can I find content for these safety meetings? Rancho Mesa wants to help provide that content. We publish a weekly landscape specific safety tailgate email. These emails arrive in your inbox every Tuesday and range from proper equipment use like “Avoiding Mower-Related Injuries,” to specific injury topics such as “Preventing Heat-Related Illness.” Our 52-week tailgate topics are not only landscape specific, but they correspond to the seasons, as well. So, you will not be receiving a topic on Heat Illness in the middle of winter, instead that topic is more likely to come out in the summer months. There are both English and Spanish versions of these tailgate topics that can be downloaded. These safety emails are something that our clients are taking full advantage of, and is a great way to take the burden of finding landscape specific safety topics off your plate, every week.
In an effort to serve and support the overall health and safety of the landscape community, we offer these trainings without charge to any landscape company that is interested in receiving them. Sign up to receive these trainings every week.
If you have any questions or would like more assistance in developing your safety program, contact me at 619-438-6905 or email me at ggarcia@ranchomesa.com.
Hydraulics Safety in the Tree Care Industry
Author, Rory Anderson, Account Executive, Rancho Mesa Insurance Services, Inc.
Tree care professionals regularly work with equipment that utilizes hydraulics: aerial lifts, stump grinders, and chippers, just to name a few. Injuries from hydraulic fluid leaks are very serious and can result in amputation.
Author, Rory Anderson, Account Executive, Rancho Mesa Insurance Services, Inc.
Tree care professionals regularly work with equipment that utilizes hydraulics: aerial lifts, stump grinders, and chippers, just to name a few.
Injuries from hydraulic fluid leaks are very serious and can result in amputation. These injuries occur when hydraulic fluid is lost through a small hole and comes in contact with the skin of a worker. The injury can at first look like a mild, small puncture wound – but the truth is that they are anything but minor.
Hydraulic fluids are toxic and act as a poison to the body. In almost all cases, treatment (surgery) is immediately required to save the workers limb.
Stump grinders, chippers, and other equipment that tree care professionals use commonly run at 4,000 PSI, and the pressure needed to penetrate your skin is only 100 PSI. So, it is vital that employees be trained on how to safely use hydraulic equipment.
Hydraulics safety trainings should include:
an overview and description of which equipment utilizes hydraulics;
proper techniques to check for leaks;
how to handle leaks;
how to handle injuries;
regular maintenance and upkeep on hydraulic hoses; and
the appropriate time to replace hydraulic hoses.
Make sure hydraulics safety is on your list of rotating topics that are regularly discussed with your crews at safety meetings.
For assistance with building your library of safety material for tailgate topics, reach out to me directly at (619) 486-6437 or randerson@ranchomesa.com.
The Construction Risk Management Guide
Author, Daniel Frazee, Executive Vice President, Rancho Mesa Insurance Services, Inc.
As a business or firm, you are most likely aware of many risks that come with construction projects. Whether it is meeting the terms of a contract, maintaining employee safety on the job site, or dealing with natural disasters, every project has its own set of hazards. If not managed, these risks can compromise your projects and prove fatal to your bottom line.
Author, Daniel Frazee, Executive Vice President, Rancho Mesa Insurance Services, Inc.
As a business or firm, you are most likely aware of many risks that come with construction projects. Whether it is meeting the terms of a contract, maintaining employee safety on the job site, or dealing with natural disasters, every project has its own set of hazards. If not managed, these risks can compromise your projects and prove fatal to your bottom line. Thus, construction risk management is a must-have for any company, but an effective plan must have easy-to-follow, yet detailed processes to help you control the risks, make decisions on how to deal with them, and turn them around to uplift your company. With the presence of rising material costs, more complex projects and increased safety concerns, having a risk management plan is more crucial than ever.
What is Construction Risk Management?
Risk management is the process of determining the risks present in your business and evaluating the procedures to minimize their impact. In the construction world, the process involves planning, monitoring and controlling instances of risk. At the center of this process is your risk management plan, a formal document that details the risks and your processes for addressing them.
Sources of construction risks may include:
Safety Risk - any risks or hazards that can lead to worker accidents at a construction site;
Financial Risk - internal and external factors like sales, problems with the economy, unexpected cost increases and competition from other firms;
Legal Risk - disputes in the fulfillment of contracts with clients;
Project Risk - hazards such as poor management of resources, miscalculation of time, lack of proper policies, etc.; and
Environmental Risk - natural phenomena that damage construction sites like floods and earthquakes.
How to Manage Risks
Before you can manage risk, companies must develop a risk management plan. This process can be broken down into six steps.
Identify the Risks
Risk identification should take place during the preconstruction phase of a project to allow ample time to manage any potential risks before accepting them. One effective way is to hold brainstorming sessions with your project team with an emphasis on identifying all the possible scenarios that could impact the project at hand. Once the brainstorm is complete, hold regular meetings to continually identify new risks that develop.Prioritize Risks in Order of Importance
High-probability risks should be handled first while low-impact, low probability risks should be addressed last. As an example, an unexpected price increase in the materials for your project can severely hurt your profit margins and might be considered a high priority.Determine your Response Strategy
Once you have evaluated the priority of risks, your team must decide a response strategy for each hazard. You can avoid the risk altogether, mitigate the risk, transfer the risk if possible via insurance and/or performance bonds, or accept the risk.Execute the Plan
Much like a sports team on game day, your company now has to execute the plan after you have developed your strategy. Your plan must detail crucial information for each team member and provide specific solutions to mitigate, transfer, or accept risks.Involve Members of the Team
Great plans are developed with multiple opinions, involving contribution from all team members typically including the ownership group, the financial officers, and the field team. Members are managing cash flows, schedules, inspections, project logs, contracts and regulatory documents.Create Contingencies and Revise
Strong risk management programs have contingency plans. That is, alternative methods for finishing a project despite accepting the risk. Consistent monitoring and revisions to your plan will help increase resilience against any possible risk and ensure that your “document” evolves and changes over time.
Benefits of Risk Management in Construction
Along with the actual building process, risk management should be seen as one of the most critical steps of a construction project. Identifying, assessing, controlling and monitoring risks strengthen awareness and teamwork among those key members of your organization. Working in step with your insurance broker for resources, templates, and feedback can be key to integrating your plan with the company’s safety initiatives. Request a sample Accident Prevention Template to start your Construction Risk Management plan. And, in turn, communicating an effective and tested plan to the insurance marketplace can position you and your broker to leverage the most competitive terms and pricing within your renewal cycle.
For more information or questions related to this article, please contact me at 619-937-0172 or via email dfrazee@ranchomesa.com.
Strengthen Your Risk Profile During COVID-19
Author, Jeremy Hoolihan, Account Executive, Rancho Mesa Insurance Services, Inc.
While the effects of COVID-19 on the workers’ compensation marketplace vary among the different business sectors, the Workers’ Compensation Insurance Rating Bureau (WCIRB) has approved a filing that will increase the 2021 pure premium advisory rates by 2.6%. With impending rate increases on the horizon, it’s more important now than ever to be proactive when it comes to your company’s risk management program. Carriers are already tightening up their underwriting guidelines and limiting schedule credits. In order to earn the most competitive pricing possible, a business must differentiate itself from other businesses. Below are three strategies you can use to strengthen your risk profile during COVID-19.
Author, Jeremy Hoolihan, Account Executive, Rancho Mesa Insurance Services, Inc.
COVID-19 continues to have a stronghold on the US economy and it is likely that we will see the impact for many years to come. While the effects of COVID-19 on the workers’ compensation marketplace vary among the different business sectors, the Workers’ Compensation Insurance Rating Bureau (WCIRB) has approved a filing that will increase the 2021 pure premium advisory rates by 2.6%. Understand that this recommended rate increase comes against a backdrop of record profits in workers’ compensation prior to COVID-19. There are also three COVID-19 presumption Bills (AB 196, AB 644, and SB 1159) that could create presumptions that cases of COVID-19 are a compensable consequence of work, which will likely cause additional turmoil in the marketplace.
With impending rate increases on the horizon, it’s more important now than ever to be proactive when it comes to your company’s risk management program. Carriers are already tightening up their underwriting guidelines and limiting schedule credits. In order to earn the most competitive pricing possible, a business must differentiate itself from other businesses. Below are three strategies you can use to strengthen your risk profile during COVID-19.
Improve the Safety Program
Now is not the time to take your focus off of safety in the workplace. In fact, I would argue that there should be even more focus on safety. Some items to focus on relating to a safety program include:
Update your Injury and Illness Protection Program (IIPP) and have it reviewed by a labor attorney.
Establish a safety committee consisting of ownership, supervisors, managers, your insurance broker, and insurance company (i.e., loss control representative). This will assist with identifying workplace hazards, discussing claims or near misses that have occurred and creating safety meeting topics that can be discussed at future employee safety meetings.
Ensure that safety meetings are occurring at least every 10 working days, but preferably weekly. Using safety topics identified by the safety committee, managers can pinpoint proper trainings for employees.
Update Employee Handbook
With employment requirements, policies and procedures continually changing, it’s easy to fall behind on new regulations like adding an Emergency Paid Sick Leave Policy or Expanded Family and Medical Leave Policy, in your employee handbook. Rancho Mesa offers access to a living handbook builder through the RM365 HRAdvantage™ portal. By creating a living employee handbook through the portal, updating the document with new policies is as easy as reviewing and approving the suggested changes provided by experienced human resources professionals.
Continue Your Risk Management Education and Certifications
With many businesses slowing during COVID-19, consider filling that down time with required accreditations and continued education courses. Some examples include:
Anti-harassment Training: By the end of 2020, businesses with 5 or more employees are required to provide Anti-harassment training to all employees. Owners, supervisors, and management are required to complete the two-hour course, while all other employees must complete a one-hour course. Rancho Mesa offers free online Anti-harassment training for both supervisors/managers and employees. The courses can be accessed by computer, tablet, and a smart phone.
Continued education or achieving professional designations: It’s also a good time to consider working on continued education courses such as renewing forklift certifications, OSHA trainings, as well as any professional designations. To reinvest your efforts in continued education, now, while business is still slow due to COVID-19, could position your business to hit the ground running when the economy opens up again.
Safety Star Certification – With underwriting guidelines tightening and worker’s compensation premiums expected to increase due to COVID-19, Rancho Mesa’s RM365 Advantage Safety Star Program™ can build your risk profile and differentiate your business from others. The program is designed for supervisors, foreman, safety coordinators, upper management, administrators, and directors of human resources. To earn the Safety Star certification in Construction Safety, you must complete the required Incident Investigation and Analysis online module plus at least two other modules of your choice from the approved list. This certification is also a marketing tool your broker can use to show your commitment to safety.
Proactively improving your safety program, employee handbook, and continuing education during the pandemic will allow you to hit the ground running once COVID-19 restrictions are lifted. It can also position your business to mitigate increasing premiums with the ever tightening workers’ compensation marketplace.
If you need any assistance in implementing a sound risk management program, please reach out to me at (619) 937-0174.
OSHA Offers Grant Programs to Nonprofits
Author, Sam Brown, Vice President, Human Services Group, Rancho Mesa Insurance Services, Inc.
Nonprofit leaders who want to make workplace safety training more accessible may be surprised to learn about a unique grant program through the Occupational Safety and Health Administration (OSHA). Since 1978, OSHA has offered grants to nonprofit organizations for safety training. Specifically, grants are awarded on a competitive basis to provide employees with training on the recognition and prevention of safety/health hazards in the workplace. The intent of the program is to reach audiences who might not otherwise receive safety training.
Author, Sam Brown, Vice President, Human Services Group, Rancho Mesa Insurance Services, Inc.
Nonprofit leaders who want to make workplace safety training more accessible may be surprised to learn about a unique grant program through the Occupational Safety and Health Administration (OSHA).
Since 1978, OSHA has offered grants to nonprofit organizations for safety training. Specifically, grants are awarded on a competitive basis to provide employees with training on the recognition and prevention of safety/health hazards in the workplace. The intent of the program is to reach audiences who might not otherwise receive safety training. OSHA renamed the program the Susan Harwood Training Grant Program, in 1997.
Grant applications in the past have typically fallen into three categories:
Capacity Building: OSHA awards these grants to help an organization grow or build its capacity to provide safety and health training to target audiences; small business employees, hard-to-reach or low-literacy workers, and workers in vulnerable and high-hazard industries.
Targeted Topic: These grants focus on occupational safety and health hazards associated with one of the OSHA selected training topics.
Training Materials Development: Grantees develop training materials on one of the OSHA selected training topics.
Although state or local government agencies are not eligible to apply, nonprofit organizations, including qualifying community and faith-based organizations, employer associations, and labor unions may submit applications.
The Harwood solicitation for grant applications can be found on the government-wide Grants.gov website.
Top 5 Free Safety Apps for Landscape Contractors
Author, Drew Garcia, Vice President, Landscape Group, Rancho Mesa Insurance Services, Inc.
Mobile devices have become an invaluable tool for many people, on the job. They provide access to contacts, email and applications (i.e., apps) that can make work a lot simpler and safer for landscapers. We researched the top apps that boost worker safety. In no particular order, here are the top 5 free safety applications for the landscape industry.
Author, Drew Garcia, Vice President, Landscape Group, Rancho Mesa Insurance Services, Inc.
Mobile devices have become an invaluable tool for many people, on the job. They provide access to contacts, email and applications (i.e., apps) that can make work a lot simpler and safer for landscapers. We researched the top apps that boost worker safety. In no particular order, here are the top 5 free safety applications for the landscape industry.
OSHA-NIOSH Heat Safety Tool
This app allows workers and supervisors to monitor the heat index for any jobsite. By utilizing the apps features any user can get a reminder about the proper safety precautions and proactive measures that should be taken under the given conditions. It is available in both English and Spanish (to access Spanish, set phone language to Spanish).
Red Cross First Aid
This app provides access to information on how to properly handle first aid emergencies. It is available in both English and Spanish.
Chemical Safety Data Sheets - ICSC
This concise app offers searchable information on substances, delivered in a simple manner. It is only available in English.
NIOSH Sound Level Meter
This app quickly monitors the level of noise exposure in order to judge and evaluate if further testing is needed. It is available in both English and Spanish.
NIOSH Ladder Safety
This interactive ladder safety application is used to assist the worker in positioning a ladder at an optimal angle. It is available in both English and Spanish.
There are many applications employers can use on devices to help improve their safety program, formalize trainings, and consolidate information.
If you use an application (with or without a fee), we would like to hear about it, so we can share with all of our safety-minded clients. Please send your feedback to Alyssa Burley, aburley@ranchomesa.com.
Promoting Safe Behaviors in the Workplace
Author, Jeremy Hoolihan, Account Executive, Rancho Mesa Insurance Services, Inc.
Safety awareness is one of the most important factors in reducing workplace injuries. There are approximately three million workplace injuries, every year. This amounts to roughly 8,000 injuries per day, 350 per hour, or 6 injuries per minute. Many of these injuries are preventable. Unsafe behaviors or decisions are usually the most common contributing factors. If employees are unaware of hazards or not motivated to follow safety protocol, their behavior will expose them even more.
Author, Jeremy Hoolihan, Account Executive, Rancho Mesa Insurance Services, Inc.
Safety awareness is one of the most important factors in reducing workplace injuries. There are approximately three million workplace injuries, every year. This amounts to roughly 8,000 injuries per day, 350 per hour, or 6 injuries per minute. Many of these injuries are preventable. Unsafe behaviors or decisions are usually the most common contributing factors. If employees are unaware of hazards or not motivated to follow safety protocol, their behavior will expose them even more.
Promoting safe behavior in the workplace can be one of the most impactful ways of reducing injuries. I encourage business owners to go above and beyond the required controls and measures such as engineering, administrative, and personal protective equipment (PPE) and promote safe behaviors and a safe work environment. Below are examples of ways ownership and management can promote safe behaviors.
Conduct frequent safety meetings with employees and encourage participation. Discuss previous injuries or near misses with your employees to identify the root cause and any corrective actions that are necessary. Be aware that not all corrective actions are readily accepted by employees, especially those seasoned employees that are set in their ways. It is important to listen to their concerns, analyze and modify the procedure or task so that the employee will buy into the changes and not be tempted to break the rules and work unsafely.
Give recognition to employees who are performing tasks safely and demonstrate proper behaviors. A little bit of recognition amongst your peers can be extremely influential and can further promote safety in the workplace.
Involve the employees in identifying and correcting hazards in the workplace. This can promote self-worth in an employee. Your employees are your eyes and ears in the field and they may identify an overlooked workplace hazard. It is especially impactful when the corrective action was a hazard they identified on their own.
Perform safety observations to encourage safe behaviors. While supervisory observations are important, business owners should also consider peer to peer safety observations. By collaborating with employees and involving them in the safety program, it will help them buy into any changes that are necessary further promoting workplace safety.
Having ownership and management consistently express their concerns for their employees well-being and safety is another way to promote safe behaviors. As a business owner, communicating to your employees that your main concern is their safety can drastically change the culture of a business. Reminding your employees that you want them to go home safely each day, goes a long way.
Promoting safe behaviors in the workplace starts with ownership and management, but is executed daily by the workforce. Providing sound policies and procedures relating to safety, along with a strong collaboration between ownership, management, and staff can drastically improve safety in the workplace and promote a safety culture.
Rancho Mesa Insurance Services, Inc. is a strong advocate for workplace safety. We like to take a risk management approach with our clients and prospects to develop a program that fits their needs. Please feel free to reach out to me, Jeremy Hoolihan, at (619) 937-0174 to see how Rancho Mesa can improve your risk profile.
Mitigating Risk at Height
Author, Casey Craig, Account Executive, Rancho Mesa Insurance Services, Inc.
Falls from elevated heights are the single most hazardous injury within the construction industry; representing 38% of all construction fatalities (NSC Construction & Utilities). That is a scary fact if you are a painting contractor that works off the ground. In years past, it was common to see painters working on multi-story scaffolding with few controls in place, or working from ladders on top of trucks to get those extra couple feet needed to finish a project. Workers compensation underwriters have difficulty with risks that work over 30 feet. Why is this 30 foot threshold so critical to insurance companies who write workers compensation?
Author, Casey Craig, Account Executive, Rancho Mesa Insurance Services, Inc.
Industry Numbers
Falls from elevated heights are the single most hazardous injury within the construction industry; representing 38% of all construction fatalities (NSC construction & utilities). That is a scary fact if you are a painting contractor that works off the ground. In years past, it was common to see painters working on multi-story scaffolding with few controls in place, or working from ladders on top of trucks to get those extra couple feet needed to finish a project. Workers compensation underwriters have difficulty with risks that work over 30 feet. Why is this 30 foot threshold so critical to insurance companies who write workers compensation?
Across the entire Construction industry, 16% of all fatal falls happened from above 30 feet (NSC Construction & Utilities).
In 2016, there were estimated to have been over 35,000 painters working in California and in total there were only 3 fatal falls (Bureau of Labor Statistics).
That accounts for less than 5% of falls, slips, or trips leading to fatality in all of California.
Mitigating Exposures: Personal Protective Equipment (PPE) and Ladder/Scaffolding Safety
As with any business that is assessing risk, start by acknowledging the potential exposures of working outside. Besides utilizing appropriate Personal Protective Equipment (PPE) for work at height, the single largest exposure for any contractor is heat exhaustion. Making sure your employees are properly hydrated and shaded is easy to overlook and can have serious consequences. Fainting at height is a serious concern and any measures that can be taken to prevent this are essential. Requiring mandatory water breaks, encouraging employees to wear loose-fitting clothes, and offering shade and protection from the sun represents tangible measures that reduce the chances of an employee suffering from heat exhaustion.
Safety equipment has become more comfortable, lighter, and easier to store and transport. Working in the heat of summer makes it difficult for employees to wear heavy equipment. This can cause them to make numerous adjustments when they are in dangerous situations. Make sure employees have light weight harnesses and are wearing them as instructed. The best PPE in the world is useless if the employees refuse to wear them properly. Similarly, it is very important to test equipment one to two times a day to ensure it is functioning properly.
Proper ladder erection and maintenance is critical for working safely at height. The recommended angle a ladder should be erected is 75 degrees. New applications such as Niosh Ladder Safety or Angel Inclination can be utilized to ensure measurements are accurate. Regular jobsite walkthroughs and inspections are also important for scaffolding. It can be fairly common that other trade contractors move or alter existing scaffolding. From day to day, objects such as connections, planks, and railing can be moved by unknown jobsite visitors and can create new fall exposures. How your safety coordinator and/or superintendents inspect and re-inspect scaffolding can literally save lives.
Turning Safe Practices into Savings
We have shared a few key tips on managing risk at height. As you design (or re-design) your fall protection program, consider how effectively your insurance broker is translating this information to the underwriters involved with your account’s renewal.
Are they clearly translating how your company mitigates risk at height?
Are they sharing key details that might separate you from another competitor?
Are they using this information to leverage competitive pricing with multiple insurance companies?
What does their information actually look like when it is sent out to an underwriter?
If these questions and this information are new to your organization, consider Rancho Mesa as an alternative. We can provide resources that can fully develop Fall Protection programs, training that can make your program actionable, and a partnership that ultimately builds the lowest cost of risk possible.
For additional information, please contact Rancho Mesa Insurance Services, Inc. at (619) 937-0164.