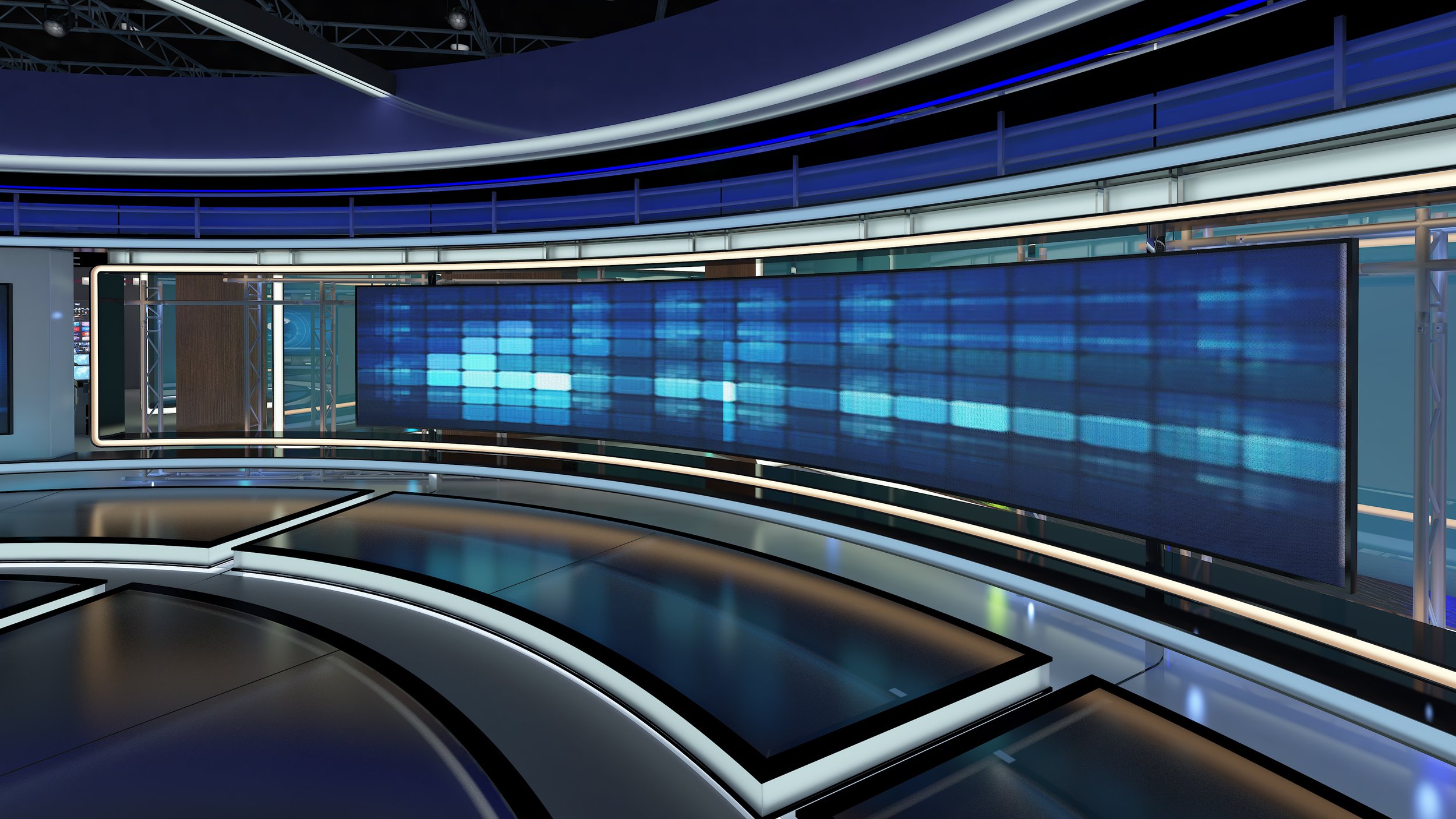
Industry News
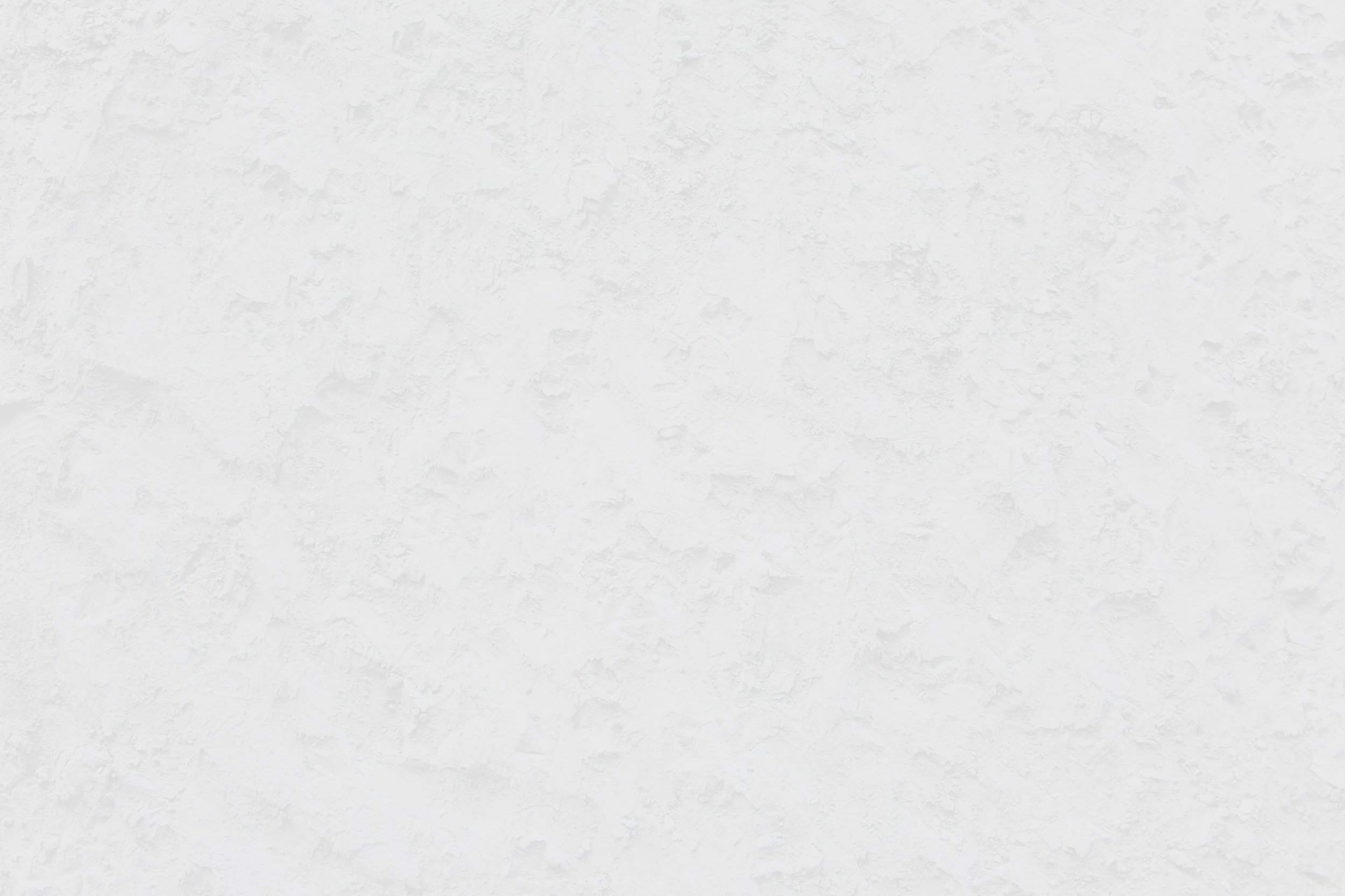
Construction Law and the Future of the Industry With Carlin Law Group
Rancho Mesa's Director of Surety Matt Gaynor interviewed Kevin Carlin of Carlin Law Group on Wednesday, March 23, 2022 to learn about his background, where he started his law career, and current hot topic’s in the construction industry. Kevin is a well-respected construction attorney here in Southern California who represents a number of Rancho Mesa clients.
Rancho Mesa's Director of Surety Matt Gaynor interviewed Kevin Carlin of Carlin Law Group on Wednesday, March 23, 2022 to learn about his background, where he started his law career, and current hot topics in the construction industry. Kevin is a well-respected construction attorney here in Southern California who represents a number of Rancho Mesa clients.
One topic of discussion centered on payment disputes.
MG: Are you seeing a lot of payment disputes right now?
KC: No, as your listeners know, the construction economy is on fire right now as there has been a ton of money sloshing around as a result of low interest rates and stimulus. While there are a few payment lawsuits going on right now, contractors seem to be more focused on getting the next job rather than chasing the money they are owed on the last job. Most of my cases right now seem to involve demands for defense and indemnity on large complex public, commercial and hospitality projects. These cases are highlighting how important, and frightening, indemnity language in prime contracts and subcontracts is, and how important it is to have good insurance. Most contracts contain indemnity language where if you are 1% at fault, you agree to pay 100% of the liability. Most people in the construction industry do not know about this or appreciate this risk because it’s never a problem until it’s a problem. These are the risks that make it so important to have the right coverages and policies of insurance, which is where you guys come in.
Listen to the full episode to learn more about Kevin and the Carlin Law Group.
How Increased Material Costs Leave Contractors Underinsured
Author, Sam Clayton, Vice President, Construction Group, Rancho Mesa Insurance Services, Inc.
Over the last 15 months, COVID-19 has brought numerous challenges to the construction industry. Second to only the labor shortage, the most pressing challenge faced by contractors is the spike in material costs which can leave them underinsured if a proper installation floater is not updated.
Author, Sam Clayton, Vice President, Construction Group, Rancho Mesa Insurance Services, Inc.
Over the last 15 months, COVID-19 has brought numerous challenges to the construction industry. Second to only the labor shortage, the most pressing challenge faced by contractors is the spike in material costs which can leave them underinsured if a proper installation floater is not updated.
Lumber, steel, copper, and other building material costs rose anywhere from 100% to 500% between April 2020 and May 2021, depending on the material. Since most projects are bid 6 to 18 months prior to the start of construction, many suppliers and subcontractors were caught off guard and did not reflect these increases in their initial bids.
Most contractors will purchase an inland marine policy that provides coverage for their miscellaneous tools, scheduled equipment, rented or leased equipment as well as an installation floater. It is important for contractors to understand the installation floater and how the increase in material costs could leave a contractor underinsured in the event of a loss.
An installation floater policy provides protection for direct physical loss or damage to materials, as well as supplies and labor costs for property being installed at jobsites. Materials are also covered while in transit and stored at temporary locations. The floater also extends coverage to the property until the installation work is accepted by the purchaser or when the insured's interest in the installed property ceases.
So, in the event of a covered loss, which includes fire, theft, explosions, transit-related damage and vandalism, a contractor’s installation floater will respond with coverage.
Proactive contractors should rely on their insurance advisor to discuss and design a program that addresses these unforeseen material and labor increases. In advance, consider the amount of product stored at any jobsite at one time, the amount of product that can be at risk in transit, the value of product stored offsite (i.e., storage units) and the protections in place that secure your product.
To discuss how an installation floater can protect your company, contact me at (619) 937-0167 or sclayton@ranchomesa.com.
Construction Industry Faces Challenges Heading into 2021
Author, Sam Clayton, Vice President, Construction Group, Rancho Mesa Insurance Services, Inc.
As a result of COVID-19’s impact on the overall economy, the construction industry will likely see some strong head winds not only operationally, but also from a risk management and insurance standpoint in 2021.
Author, Sam Clayton, Vice President, Construction Group, Rancho Mesa Insurance Services, Inc.
As a result of COVID-19’s impact on the overall economy, the construction industry will likely see some strong head winds not only operationally, but also from a risk management and insurance standpoint in 2021.
Construction contractors are likely to feel the effects of economic uncertainty, insurance premium increases and labor storages moving forward. Specifically, when planning for 2021, contactors should consider:
Economic Uncertainty
Funds may not be available as city, state and federal budgets are reduced.
Projects may be delayed or canceled.
Your back log of projects may be reduced.
Surety companies may implement tighter requirements.
Insurance Impacts
The commercial insurance market may harden causing increased premiums.
Insurance carriers may have a limited capacity as they have been affected by the pandemic and natural disasters.
New exclusions may be added as policies are renewed.
Labor Force Decreases
Employment Practices Liability (EPL) Exposure may increase as new and/or inexperienced employees are hired.
As we move into 2021 and begin to face these challenges, we’ve developed the following steps and actions you can take to help minimize these concerns:
Economic Uncertainty
Audit your existing backlog and determine which projects may experience delays or cancellations.
Review and audit your existing surety program to make sure you have adequate capacity to meet your present and future surety needs. Rancho Mesa’s Surety department has a best practices audit program to assess your needs. Complete an interest form and our team will be able to assist you.
Insurance Impacts
Meet with your insurance advisor and start the renewal process 90-120 days prior to your renewal.
With your insurance advisor, review all new coverage changes, conditions, and exclusions that will impact your risk management program.
Accurately project your rating basis (field payroll/sales) that will affect your workers’ compensation, general liability and excess insurance premiums.
Labor Force Decreases
Use best practices during any labor reductions to limit EPL exposures like wrongful termination, discrimination, etc.
Through Rancho Mesa’s RM365 HRAdvantage™ Portal, clients have access to a library of resources and 50 human resources consultants to answer your questions and provide you information in making those decisions.
To discuss your 2021 risk management plans, contact me at (619) 937-0167 or sclayton@ranchomesa.com.
Equipment Hazards and Ways to Reduce Exposure
Author, Daniel Frazee, Executive Vice President, Rancho Mesa Insurance Services, Inc.
The very nature of the construction business creates risk; from injuries in the course of employment, damage to property, third party liability, etc. One important area that can be overlooked is equipment security. While there is simply no way to eliminate 100% of risk to equipment, there are several steps a contractor can take to initiate proper controls and minimize losses in this area.
Author, Daniel Frazee, Executive Vice President, Rancho Mesa Insurance Services, Inc.
The very nature of the construction business creates risk - from injuries in the course of employment, damage to property, third party liability, etc. One important area that can be overlooked is equipment security. While there is simply no way to eliminate 100% of risk to equipment, there are several steps a contractor can take to initiate proper controls and minimize losses in this area.
Managing Keys and Locks
Locks should be placed on all vehicles, storage sheds, portable equipment, and trailers. It is recommended that “high security” locks, which are pick-resistant or laminated in steel, be used in all cases. Chains should be case-hardened and thick enough to prevent cutting. Many contractors also use locking fuel caps on vehicles and passive alarm systems, for higher valued machinery, to disable equipment or sound an alarm when there is attempted theft.
Operating or Transporting Equipment
Drivers and/or operators of equipment must be screened prior to use. Requiring a valid driver’s license is a good start, but also consider asking for medical history, criminal background check, motor vehicle record, random drug screens, and sight and hearing checks. Employees should be trained properly in company safety procedures, rules, and emergency protocol. In loading or unloading situations, consider the angle of the ramp, how your employees are stabilizing the piece of equipment, placement of flags, and ensuring the ignition and brakes are locked.
Construction Site Security
Construction sites have always been attractive targets for thieves. The considerable value of equipment, product, tools, and machinery create strong appeal, particularly if that location is not properly secured. Stepping up the security at a jobsite can come in many forms but several best practice methods stand out. They include securing a specific area within the site for equipment storage. The more difficult it is for a thief to access equipment, the less motivated they will be to take the risk of accessing the site. Maintaining an equipment inventory control with photographs and “check-out” systems can be critical to holding employees accountable. Lastly, and perhaps the most logical task to improve security on a jobsite, are regular inspections. These can occur from superintendents, owners, managers, etc. This oversight shows all contractors performing work that your equipment is important and you are managing it regularly.
Fire Prevention
Managing the exposure to fuel is an important first step for preventing fire losses of equipment on a jobsite. Engaging an outside vendor to provide fueling services is always a possible solution, but may not be realistic. If the contractor is responsible for their own fueling, consider the flammability of different fuels, location of onsite fuel supplies, tank inspection, and methods for clean-up and disposal of the fuel. Regular intervals of visual inspections by the operator and any ensuing maintenance allow for easy fixes or repairs that minimize the development of bigger issues.
As the construction industry continues reaching strong post-recession levels, the use of equipment from trade and general contractors, across the board, is more prevalent. Developing a “safety net” around jobsites, pre-qualifying those using equipment, and prioritizing theft and fire mitigation lower your organization’s overall risk. Take some or all of the ideas above as your first step in integrating equipment security into your overall safety plan.
For additional information, please contact Rancho Mesa Insurance Services, Inc. at (619) 937-0164.